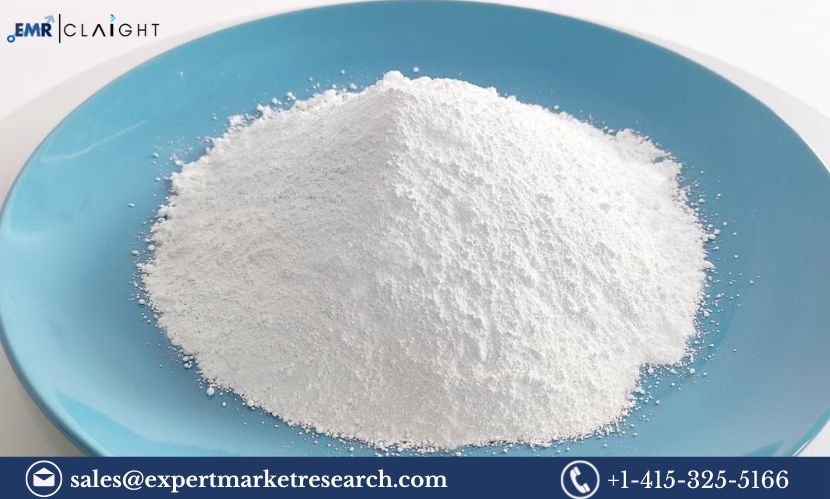
Introduction
Zinc sulfite, also known as zinc bisulfite, is a versatile chemical compound widely used in industries such as textiles, water treatment, pharmaceuticals, and agriculture. It plays an essential role as a reducing agent, bleaching agent, and an intermediate in the synthesis of other chemicals. The Zinc Sulfite Manufacturing Plant Project Report provides a detailed roadmap for setting up a manufacturing plant focused on the production of zinc sulfite. This report covers essential aspects of the manufacturing process, required raw materials, machinery, financial considerations, market demand, and other critical factors that entrepreneurs and investors need to understand before embarking on a zinc sulfite manufacturing venture.
Zinc sulfite is particularly in demand in industries that rely on its reducing properties and in processes such as metal extraction, water treatment, and the production of specialty chemicals. The increasing applications and growing need for zinc-based chemicals make establishing a manufacturing plant for zinc sulfite a promising opportunity.
What is Zinc Sulfite?
Zinc sulfite is a chemical compound with the formula ZnSO₃, often available as a white crystalline powder or a colorless solution. It is formed by the reaction of zinc oxide or zinc metal with sulfur dioxide (SO₂). Zinc sulfite is used in various industrial applications due to its versatile properties, including:
- Reducing Agent: Zinc sulfite is widely used as a reducing agent in chemical processes.
- Water Treatment: It is used in water treatment processes for removing heavy metals and purifying water.
- Textile Industry: Zinc sulfite is used in the textile industry for bleaching and whitening fabrics.
- Photography: Historically, it was used in photographic solutions as a reducing agent.
- Agriculture: Zinc sulfite finds applications in agriculture as a pesticide and in soil treatments to improve crop yield.
The increasing demand for high-quality zinc sulfite across these industries presents significant opportunities for manufacturers.
Get a Free Sample Report with Table of Contents@
Market Demand and Growth Prospects
The demand for zinc sulfite is growing globally due to its wide range of applications in several key industries. The following factors contribute to the market growth:
1. Textile Industry Growth
Zinc sulfite is used extensively in the textile industry for bleaching and whitening fabric. The growing global demand for textiles, driven by population growth and increased urbanization, is expected to continue driving the need for zinc sulfite in textile processing.
2. Water Treatment and Environmental Concerns
The rising concern over water pollution and the growing demand for clean water is propelling the demand for water treatment chemicals. Zinc sulfite is used in water treatment to remove impurities such as heavy metals and to purify industrial effluents, making it a critical component in environmental protection and pollution control.
3. Agriculture and Pesticides
Zinc sulfite is also utilized in agriculture to improve soil quality and protect crops from pests and diseases. As the global population increases and the need for higher agricultural output grows, zinc sulfite’s use as a soil conditioner and pesticide will likely expand.
4. Pharmaceutical and Chemical Industries
Zinc sulfite’s role as an intermediate in the production of other chemicals and in pharmaceuticals also contributes to its steady demand. The growing pharmaceutical and chemical sectors, especially in emerging economies, will further fuel the need for zinc sulfite in the coming years.
Key Components of a Zinc Sulfite Manufacturing Plant
Setting up a zinc sulfite manufacturing plant involves several crucial elements. The following sections cover the required raw materials, production process, machinery, and staffing considerations.
1. Raw Materials
The key raw materials required for the production of zinc sulfite include:
- Zinc Oxide or Zinc Metal: Zinc oxide (ZnO) or zinc metal (Zn) serves as the primary zinc source for zinc sulfite production.
- Sulfur Dioxide (SO₂): Sulfur dioxide gas is the main reagent for the reaction that produces zinc sulfite.
- Water: Water is required for the chemical reaction and to control the process parameters.
- Acids: In some variations of the production process, acids may be used to control pH levels.
The sourcing of high-quality raw materials is critical for ensuring the consistent quality and purity of the zinc sulfite produced.
2. Production Process
The production of zinc sulfite involves a simple chemical reaction between zinc oxide (or zinc metal) and sulfur dioxide gas:
Reaction Between Zinc and Sulfur Dioxide
The reaction takes place in a controlled environment, where sulfur dioxide gas is bubbled through water or a solution containing zinc oxide or zinc metal. The chemical reaction is as follows:
ZnO+SO2→ZnSO3text{ZnO} + text{SO}_2 rightarrow text{ZnSO}_3
This process can also occur with zinc metal, leading to the formation of zinc sulfite. The reaction produces zinc sulfite as a precipitate, which is then filtered and purified.
Purification and Filtration
After the reaction, the resulting zinc sulfite is typically a wet slurry or precipitate. The next step involves separating the solid zinc sulfite from the liquid by filtration. The filtered zinc sulfite is then washed to remove any impurities and to ensure purity.
Drying Process
The filtered and washed zinc sulfite is then dried to remove any remaining moisture. Drying is typically done using a rotary dryer or other industrial drying equipment. The dried zinc sulfite is then ready for packaging or further processing, depending on the intended application.
Packaging
Once the zinc sulfite is dried and cooled, it is packaged in moisture-resistant bags or containers. Packaging is crucial for preserving the quality of the product and ensuring its safe transportation.
3. Machinery and Equipment
The key machinery required for zinc sulfite manufacturing includes:
- Reactor Vessels: For carrying out the reaction between zinc oxide and sulfur dioxide.
- Filtration Units: For separating zinc sulfite from the reaction mixture.
- Drying Equipment: Rotary dryers or fluidized bed dryers are used to dry the zinc sulfite to a moisture content suitable for packaging.
- Packaging Machines: For packaging the final product in moisture-resistant containers or bags.
- Mixing and Blending Units: For mixing raw materials and controlling the consistency of the reaction.
Investing in high-quality, efficient machinery is essential to ensure that the manufacturing process is cost-effective and produces high-quality zinc sulfite.
4. Labor and Staffing
The staffing requirements for a zinc sulfite manufacturing plant include:
- Chemical Engineers: To oversee the chemical processes and ensure that production meets quality standards.
- Machine Operators: Skilled operators are required to run the equipment and manage day-to-day operations.
- Quality Control Personnel: To test the finished product for purity, consistency, and compliance with industry standards.
- Maintenance Crew: To ensure that all machinery is functioning properly and is well-maintained to minimize downtime.
- Administrative Staff: To handle logistics, procurement, and customer relations.
Financial Considerations and Investment
1. Initial Investment
Setting up a zinc sulfite manufacturing plant involves significant capital investment. The key cost components include:
- Plant Setup: Purchasing or leasing land, constructing buildings, and setting up utilities such as water, electricity, and waste management systems.
- Machinery and Equipment: Acquiring reactors, dryers, filtration units, and packaging machines.
- Raw Materials: Initial procurement of zinc oxide, sulfur dioxide, and other required chemicals.
- Labor Costs: Hiring and training skilled personnel to operate machinery and manage operations.
2. Operating Costs
Once the plant is operational, ongoing costs will include:
- Raw Materials: Continuous sourcing of zinc oxide and sulfur dioxide.
- Energy: The energy required for the reaction process, drying, and other manufacturing steps.
- Labor: Salaries for employees, including machine operators, engineers, and quality control personnel.
- Maintenance: Regular maintenance of machinery to ensure smooth operations and avoid disruptions.
3. Revenue Generation
Revenue will be generated from the sale of zinc sulfite to industries such as textiles, water treatment, agriculture, and pharmaceuticals. Pricing will depend on factors like production volume, market demand, and product quality.
4. Profitability and ROI
Profitability will depend on factors such as production efficiency, raw material costs, and market demand. A well-managed plant can achieve high profitability by optimizing operations and ensuring high product quality.
Regulatory Compliance and Environmental Considerations
1. Safety Standards
Given the chemicals involved in the production of zinc sulfite, it is crucial to comply with safety regulations to protect workers and the environment. Adequate personal protective equipment (PPE) and safety protocols should be in place to minimize the risk of exposure to harmful chemicals.
2. Environmental Impact
The production of zinc sulfite can generate waste, including sulfur dioxide emissions and chemical byproducts. Implementing waste management strategies, such as capturing and neutralizing sulfur dioxide emissions, and recycling materials, can help reduce the environmental impact.
Media Contact
Company Name: Claight Corporation
Contact Person: Lewis Fernandas, Corporate Sales Specialist — U.S.A.
Email: sales@expertmarketresearch.com
Toll Free Number: +1–415–325–5166 | +44–702–402–5790
Address: 30 North Gould Street, Sheridan, WY 82801, USA
Website: www.expertmarketresearch.com
Aus Site: https://www.expertmarketresearch.com.au
Leave a Reply