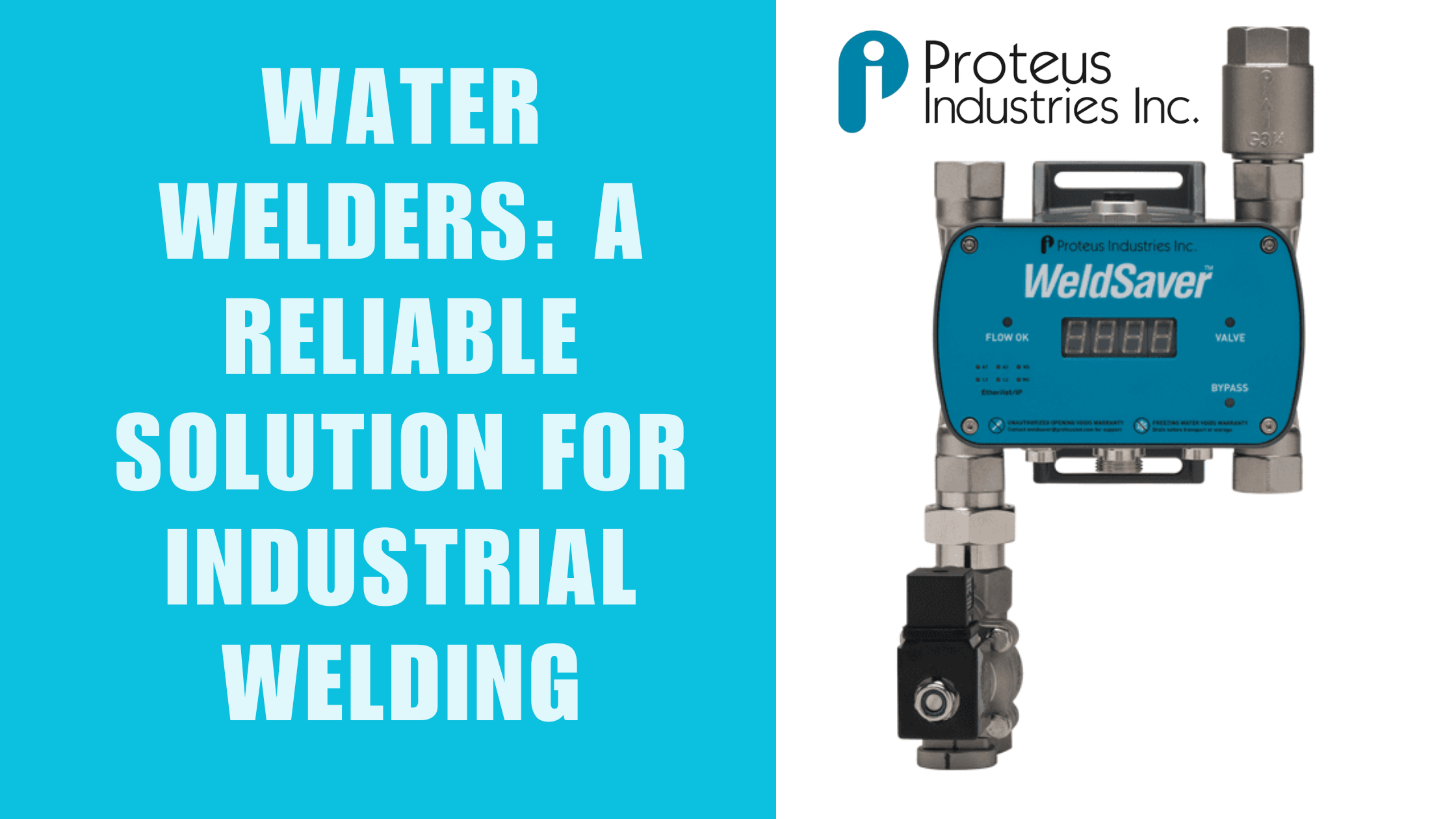
In the fast-paced world of industrial welding, precision, efficiency, and safety are essential. While effective, traditional welding methods often have challenges, including heat distortion, longer setup times, and increased energy consumption. However, with the advent of water welders, industries are now experiencing a breakthrough in welding technology that offers enhanced benefits. These tools are not just changing how welding is done; they are revolutionizing it. In this article, we will explore everything you need to know about water welders in an industrial context. We will dive into their working mechanism, benefits, applications, and why they are quickly becoming a go-to industrial welding solution.
What Are Water Welders?
Water welders are advanced welding machines that use water as a cooling agent to prevent excessive heat buildup during welding. Traditional welding generates a lot of heat, which can cause warping, distortion, and damage to the surrounding material. Water welders eliminate this issue by using a water-cooled electrode or nozzle that reduces heat exposure, ensuring a clean, precise weld without damaging the base material. The cooling mechanism in water welders allows for faster weld solidification, resulting in quicker turnaround times and greater efficiency. These welders are designed to offer high performance with low energy consumption, making them an eco-friendly and cost-effective option for industrial applications.
How Do Water Welders Work?
At the heart of every water welder is a cooling system that utilizes water to maintain the temperature of the electrode or welding arc. This is critical because overheating the electrode can force it to break or wear out prematurely. Traditional welding methods often deal with this issue by using additional cooling fans or larger power systems. However, water welders have a built-in water circulation system that regulates the temperature directly at the point of contact.
The cooling system involves circulating water through the welding nozzle or electrode. This process helps maintain the temperature at optimal levels, preventing overheating and ensuring the surrounding metal does not distort or warp. This system allows operators to work with delicate materials or high-strength alloys without fear of damaging the workpiece, a significant advantage in industrial welding.
The Advantages of Water Welders in Industrial Applications
There are several reasons why water welders are quickly gaining popularity in the industrial sector. Below are some of the primary advantages of incorporating these tools into your industrial welding processes:
1. Improved Precision and Quality
One of the standout features of water welders is their ability to offer high precision. Since the heat is controlled so carefully, the risk of distortion or warping is minimized. This ensures the welds are smooth, uniform, and of the highest quality. In industries where precision is critical, such as automotive or aerospace, water welders provide the ideal solution for creating parts that meet stringent standards.
2. Energy Efficiency
Traditional welding methods require a lot of energy, especially for heavy-duty tasks. Water welders are designed to consume less power by maintaining a consistent temperature throughout welding. This energy efficiency rules lower electricity bills and a reduced carbon footprint, making water welders a more sustainable choice for industrial applications.
3. Reduced Environmental Impact
The environmentally friendly aspect of water welders cannot be overstated. Since these tools use water instead of additional chemicals or gases for cooling, they contribute to fewer emissions and waste materials. Additionally, they are highly energy-efficient, helping to reduce the overall environmental impact of industrial welding operations.
4. Faster Welding Process
The efficient cooling system in water welders allows for quicker solidification of the weld. Workers can complete their tasks more rapidly, increasing throughput in industrial settings. Faster welding times also mean less time is spent on equipment setup, maintenance, and repairs, contributing to overall operational efficiency.
5. Improved Safety
Welding can be hazardous, especially when dealing with excessive heat and potentially dangerous sparks. Water welders minimise the risk of burns, fire hazards, and other safety issues. Reduced heat exposure means a safer working environment for welders, lowering the likelihood of workplace accidents and injuries.
How to Choose the Right Water Welder for Your Industrial Needs
When selecting a water welder for your industrial operation, several factors must be evaluated to ensure the best fit. Here are some key factors to keep in mind:
1. Power Requirements
The power capacity of the water welder should align with the types of materials you plan to weld. You’ll need a heavier-duty welder with higher power levels, while lighter jobs may only require a lower-powered machine.
2. Welding Material
Different water welders are designed for specific materials like steel, aluminium, or titanium. To achieve the best results, selecting a welder that is consistent with the materials used in your industry is essential.
3. Weld Size and Thickness
Consider the size and thickness of the welds you’ll be working on. If your industrial needs involve significant welds or thick materials, you will need a machine capable of handling such requirements without compromising quality.
4. Ease of Use
The more intuitive and user-friendly a water welder is, the easier it is for operators to achieve consistent results. Look for models with straightforward controls and easy maintenance features to streamline your welding processes.
The Future of Water Welders in Industrial Welding
As industries continue to grow and demand higher levels of precision, sustainability, and efficiency, water welders are balanced to play an increasingly significant role in the future of welding. Innovations in welding technology, such as enhanced cooling systems and improved power management, will make water welders even more efficient and accessible for industrial operations of all sizes.
Proteus Industries Inc., a leader in the welding equipment industry, continues to push the envelope with its water welding technology. With their dedication to quality and invention, we can expect even more significant advancements in water welders in the coming years.
Conclusion
Water welders offer numerous advantages to industrial operations, including improved precision, faster welding times, energy efficiency, and enhanced safety. Whether in automotive manufacturing, aerospace, construction, or electronics, using water welders can significantly improve the quality and speed of your welding processes. As technology advances, water welders will continue to provide a reliable and endurable solution for industries looking to enhance their welding capabilities. Investing in water welders from reputable companies like Proteus Industries Inc. ensures that your operations remain efficient, safe, and environmentally friendly.
Leave a Reply