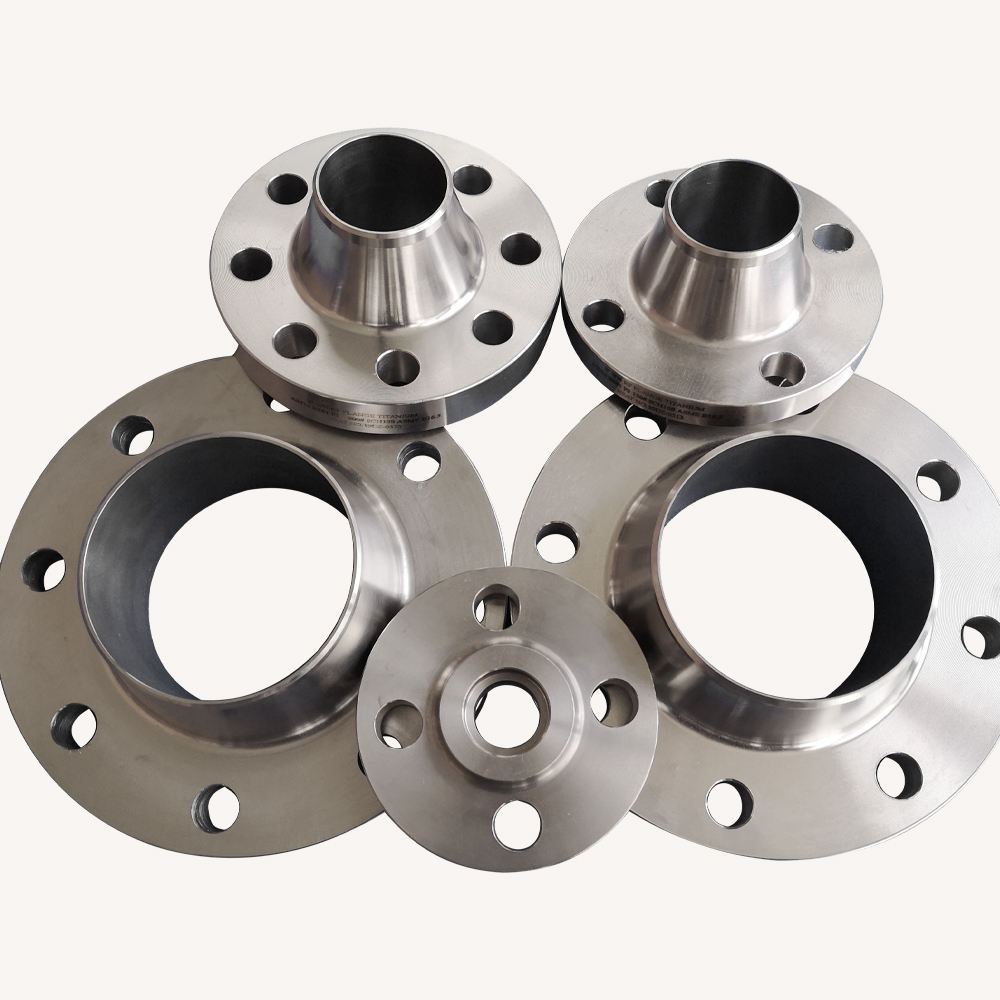
Titanium flanges are widely used in industries that require high strength, corrosion resistance, and lightweight materials. These flanges play a crucial role in connecting pipes, valves, and pumps in piping systems. However, not all titanium flanges are the same. Different grades of titanium offer varying mechanical properties and corrosion resistance, making them suitable for specific applications.
In this guide, we will explore the different grades of Titanium Flanges, their characteristics, and how to choose the right Titanium Flanges Manufacturer for your needs.
What Are Titanium Flanges?
Titanium flanges are pipe fittings made from titanium alloys, designed to provide secure connections in piping systems. They are highly valued for their excellent strength-to-weight ratio, resistance to extreme temperatures, and superior corrosion resistance. These flanges are commonly used in aerospace, marine, chemical processing, and medical industries.
Different Grades of Titanium Flanges
Titanium is classified into different grades based on its composition and properties. The most commonly used grades for flanges include:
1. Titanium Grade 1 Flanges
- Characteristics:
- Pure titanium with the highest ductility.
- Excellent corrosion resistance in oxidizing and mildly reducing environments.
- Soft and easily formable.
- Applications:
- Marine and chemical processing industries.
- Heat exchangers and desalination plants.
2. Titanium Grade 2 Flanges
- Characteristics:
- Most widely used commercially pure titanium grade.
- Excellent weldability and moderate strength.
- Good resistance to seawater and acidic environments.
- Applications:
- Aerospace, marine, and power generation.
- Chemical processing and medical implants.
3. Titanium Grade 3 Flanges
- Characteristics:
- Higher strength than Grade 2 but lower ductility.
- Good corrosion resistance in aggressive environments.
- Ideal for applications requiring increased mechanical strength.
- Applications:
- Aerospace and structural applications.
- Pressure vessels and heat exchangers.
4. Titanium Grade 5 Flanges (Ti-6Al-4V)
- Characteristics:
- Alloyed with aluminum and vanadium for enhanced strength.
- Excellent heat resistance and corrosion resistance.
- Most commonly used titanium alloy in industrial applications.
- Applications:
- Aerospace components and marine structures.
- Medical implants and high-performance racing parts.
5. Titanium Grade 7 Flanges
- Characteristics:
- Similar to Grade 2 but with added palladium for better corrosion resistance.
- Superior performance in acidic environments.
- Applications:
- Chemical and desalination plants.
- High-corrosion environments with acidic exposure.
6. Titanium Grade 9 Flanges (Ti-3Al-2.5V)
- Characteristics:
- Lower aluminum and vanadium content compared to Grade 5.
- Good formability and corrosion resistance.
- Commonly used in high-performance applications.
- Applications:
- Aerospace and sports equipment manufacturing.
- Hydraulic tubing and marine applications.
7. Titanium Grade 12 Flanges
- Characteristics:
- Enhanced strength and corrosion resistance.
- Can withstand high temperatures and aggressive environments.
- Applications:
- Power plants and chemical processing.
- Heat exchangers and marine equipment.
Advantages of Using Titanium Flanges
Titanium flanges offer several benefits over traditional materials like stainless steel and carbon steel. Some of the key advantages include:
1. Exceptional Corrosion Resistance
Titanium naturally forms an oxide layer that protects it from rust and corrosion, making it ideal for harsh environments.
2. High Strength-to-Weight Ratio
Titanium flanges provide excellent strength while being significantly lighter than steel, making them perfect for weight-sensitive applications.
3. Excellent Heat Resistance
Titanium can withstand extreme temperatures, making it suitable for aerospace, power plants, and chemical processing applications.
4. Biocompatibility
Titanium is non-toxic and safe for use in medical and food processing industries.
5. Long Service Life
Due to their durability and corrosion resistance, titanium flanges have a longer lifespan, reducing maintenance and replacement costs.
How to Choose the Right Titanium Flanges Manufacturer?
Selecting a trusted Titanium Flanges Manufacturer is crucial to ensuring quality and reliability. Here are some factors to consider:
1. Certification and Quality Standards
Ensure the manufacturer meets international standards such as ASTM, ASME, and ISO certifications for high-quality products.
2. Material Testing and Inspection
A reputable manufacturer should provide material test certificates (MTC) and third-party inspection reports to guarantee product quality.
3. Customization Options
Check if the manufacturer offers custom-sized flanges to meet your specific project requirements.
4. Competitive Pricing
Compare prices from different suppliers to find a balance between cost and quality.
5. Customer Support and Delivery Time
Choose a manufacturer with excellent customer service and a proven track record of timely deliveries.
Conclusion
Understanding the different grades of Titanium Flanges helps in selecting the right type for your specific application. Whether you need corrosion resistance for marine environments, high strength for aerospace, or biocompatibility for medical use, titanium offers unmatched advantages.
When sourcing titanium flanges, working with a reliable Titanium Flanges Manufacturer ensures you receive high-quality, certified products that meet industry standards.
If you’re looking for premium titanium flanges, choose a trusted supplier that guarantees durability, performance, and compliance with international standards.
Leave a Reply