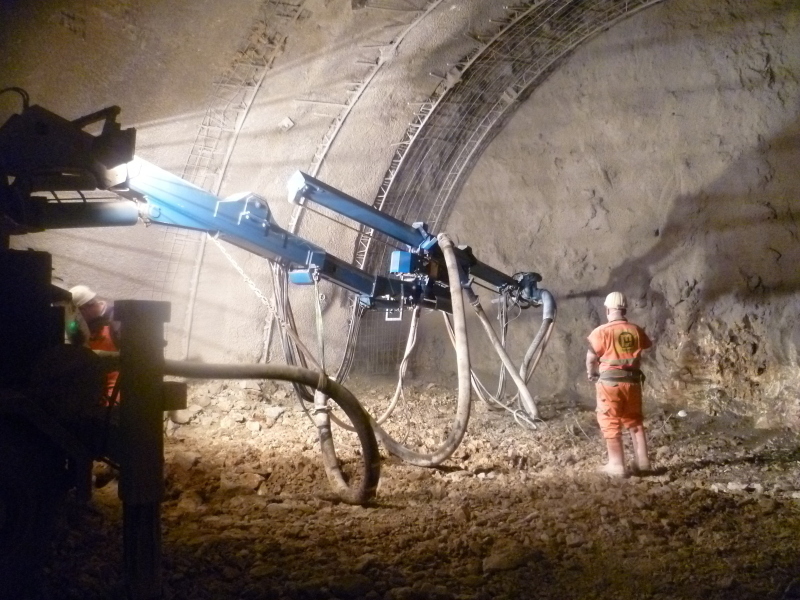
Shotcrete Underground mining and tunnel construction are among the most challenging engineering feats, requiring innovative solutions to ensure stability and safety. Shotcrete has emerged as a critical tool in these environments, providing durable and efficient support systems. Combined with advanced safety practices, shotcrete is revolutionizing the way we protect workers and infrastructure underground.
Shotcrete in Underground Mining
In underground mining, maintaining stable rock surfaces is paramount. Shotcrete—sprayed concrete—is applied to surfaces to provide immediate support and prevent collapses.
Why Shotcrete is Essential in Mining:
- Rapid Application: Shotcrete can be applied quickly, reducing the risk of delays and ensuring worker safety.
- Surface Stabilization: Creates a durable layer that prevents loose rock from falling in active mining areas.
- Versatility: Adapts to irregular surfaces, making it ideal for mine shafts, tunnels, and chambers.
- Cost-Effective: Reduces the need for extensive support structures, saving time and resources.
Applications of Shotcrete in Mining:
- Tunnel Linings: Provides a strong, protective coating to tunnel walls and ceilings.
- Rock Bolt Encapsulation: Works in tandem with rock bolts for enhanced stability.
- Reinforcement of Stopes: Ensures the structural integrity of mining excavations.
- Sealing and Waterproofing: Prevents water ingress, which can weaken rock formations.
Tunnel Safety: Beyond Stability
In both mining and civil projects, ensuring tunnel safety goes beyond preventing collapses. Modern safety practices prioritize worker protection, structural resilience, and environmental sustainability.
Key Factors in Tunnel Safety:
- Structural Integrity: Shotcrete plays a vital role in reinforcing weak rock masses and stabilizing tunnel walls.
- Ventilation Systems: Proper airflow reduces exposure to harmful gases and dust.
- Fire Resistance: Shotcrete can be formulated with fire-resistant properties to protect workers and equipment in emergencies.
- Monitoring and Inspections: Regular checks ensure early detection of potential hazards, such as cracks or water seepage.
- Lighting and Signage: Well-lit tunnels with clear signage improve navigation and reduce accidents.
How Shotcrete Enhances Tunnel Safety
Shotcrete directly contributes to tunnel safety by addressing structural and environmental challenges:
- Prevents Rockfalls: The high-strength material bonds securely to rock surfaces, minimizing the risk of loose debris.
- Customizable Properties: Adjusting the mix allows for additional features like fire resistance or rapid setting for emergencies.
- Dust Suppression: Wet-mix shotcrete reduces dust levels during application, improving air quality for workers.
- Durability: Resistant to cracking, water ingress, and harsh underground conditions, ensuring long-lasting protection.
Choosing the Right Solutions for Your Project
The success of any underground mining or tunneling project relies on using the right combination of materials, equipment, and expertise.
- Shotcrete Mix: Select the appropriate wet or dry mix based on project requirements.
- Application Method: High-quality shotcrete machines ensure efficient and even application.
- Safety Measures: Implement robust monitoring systems and train workers on safety protocols.
Conclusion
The combination of shotcrete and modern tunnel safety practices is transforming underground mining and tunneling. These advancements not only protect workers but also enhance the efficiency and longevity of critical infrastructure.
If you’re planning an underground project, investing in the right shotcrete solutions and safety systems is non-negotiable. Contact us today to learn more about how we can help you achieve optimal results while prioritizing safety and durability.
Leave a Reply