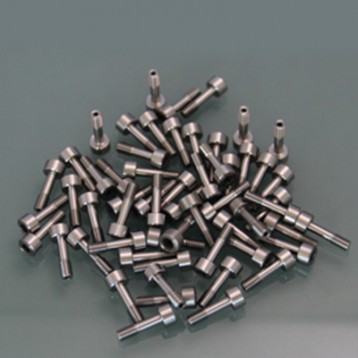
Screw precision parts are essential components in various industries, ranging from automotive and aerospace to medical and consumer electronics. These meticulously crafted fasteners play a crucial role Screw Precision Parts in ensuring the stability, durability, and reliability of assemblies. Their precision engineering allows for exacting tolerances, making them indispensable in high-performance applications.
What Are Screw Precision Parts?
Screw precision parts are specially manufactured screws designed to meet stringent specifications in terms of dimensions, material composition, and threading. These parts are created using advanced machining techniques such as CNC (Computer Numerical Control) turning, Swiss machining, and thread rolling to achieve consistent and accurate results.
Materials Used in Precision Screws
The choice of material is vital in determining the functionality and longevity of precision screws. Common materials include:
- Stainless Steel – Corrosion-resistant and ideal for medical and marine applications.
- Titanium – Lightweight yet strong, often used in aerospace and medical implants.
- Brass – Known for its electrical conductivity, used in electronic and electrical components.
- Aluminum – Lightweight and resistant to oxidation, making it suitable for automotive and aerospace industries.
- Alloy Steel – Offers enhanced strength and durability, commonly used in industrial machinery.
Manufacturing Process of Precision Screws
The production of screw precision parts involves multiple steps, ensuring that each piece meets exact specifications:
- Material Selection – Choosing the right material based on application requirements.
- Machining – CNC turning and Swiss machining techniques are used to shape the screw with high precision.
- Thread Cutting or Rolling – Threads are meticulously crafted to ensure proper engagement and secure fastening.
- Surface Treatment – Various coatings such as anodizing, galvanizing, and black oxide are applied to enhance corrosion resistance and durability.
- Quality Control – Each batch undergoes rigorous inspection using coordinate measuring machines (CMM), optical comparators, and thread gauges to ensure dimensional accuracy.
Applications of Precision Screws
Precision screws are widely used in various industries, including:
- Automotive – Engine components, transmission assemblies, and electronic control units.
- Aerospace – High-strength fasteners for aircraft frames, turbines, and navigation systems.
- Medical – Surgical implants, orthopedic devices, and dental implants.
- Electronics – Circuit boards, mobile devices, and precision instruments.
- Industrial Machinery – Heavy-duty fastening for robotics, automation, and tooling equipment.
Advantages of Using Precision Screws
Investing in precision screws offers several benefits, such as:
- High Accuracy – Ensures perfect fit and alignment in assemblies.
- Enhanced Durability – Made from high-quality materials that resist wear and corrosion.
- Improved Performance – Reduces mechanical failures due to poor fastener quality.
- Customization Options – Can be tailored to specific industry needs with various head types, threading styles, and coatings.
Conclusion
Screw precision parts are the unsung heroes of modern engineering, enabling the seamless operation of countless applications. Their role in enhancing structural integrity, reliability, and efficiency makes them a crucial component across multiple industries. With continuous advancements in machining technology, precision screws are set to become even more refined, supporting the future of engineering innovation.
Leave a Reply