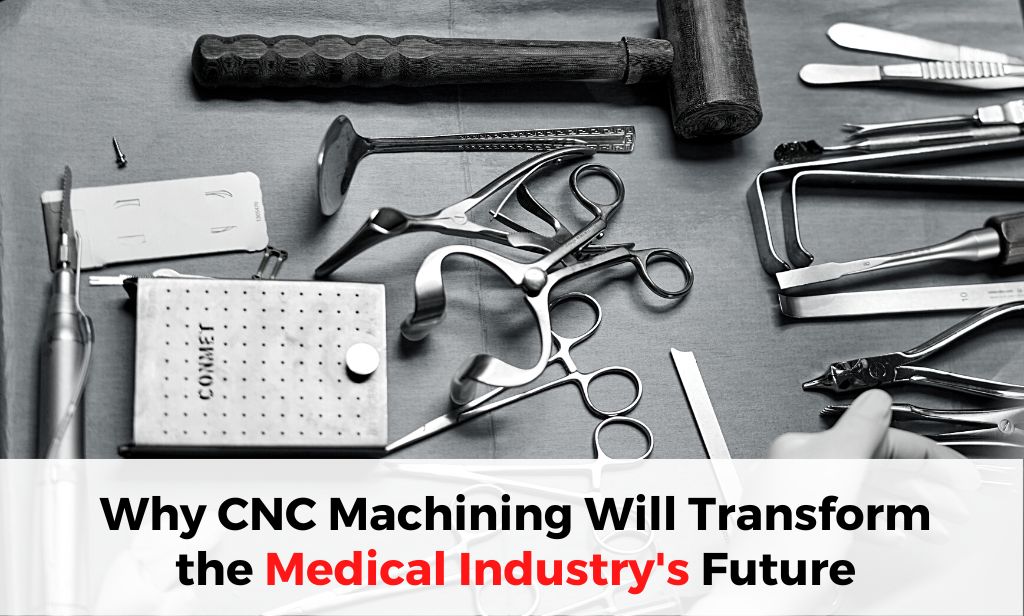
In the world of healthcare, precision is paramount. From surgical instruments to implants, the quality and accuracy of medical devices directly affect the outcome of patient treatments. As a result, the manufacturing of these critical components requires the highest level of precision, which is where Medical CNC (Computer Numerical Control) machining plays an essential role.
Medical CNC machining involves the use of automated machines controlled by computers to manufacture medical devices, parts, and components with exceptional accuracy and repeatability. Over the years, Medical CNC technology has revolutionized the healthcare industry by allowing manufacturers to produce highly complex, custom, and precise parts at scale.
This article will explore the role of Medical CNC machining in the medical field, its benefits, common applications, and how it continues to advance the quality and efficiency of healthcare devices and systems.
What is Medical CNC?
Medical CNC refers to the use of CNC machining technology specifically applied to the production of medical devices, equipment, and components. CNC machines are automated tools that use computer programs to control the movement of tools and machines in the manufacturing process. The high precision and control offered by CNC technology are crucial for the production of medical products, which often need to meet stringent regulations and exacting standards.
In the medical industry, CNC machining is used to produce a variety of products, ranging from small, delicate surgical instruments to large, life-saving implants. The versatility and efficiency of CNC machining make it an ideal method for manufacturing products that require precise dimensions, intricate designs, and consistent performance.
The Role of CNC in Healthcare
CNC machines are used to manufacture a wide range of medical devices and components, including:
- Surgical instruments: Scalpels, forceps, clamps, and other tools used in surgeries require precise manufacturing to ensure safety and functionality.
- Medical implants: Artificial joints, dental implants, and other prosthetics are commonly produced using CNC machining, as these parts must meet exact specifications for optimal fit and function.
- Diagnostic equipment: Components of diagnostic machines such as MRI machines, X-ray devices, and ultrasound equipment are also manufactured with the help of CNC technology.
- Orthopedic devices: Parts such as bone plates, screws, and implants used in orthopedics are manufactured with extreme precision using CNC machining.
How Does Medical CNC Work?
CNC machining in the medical field operates in much the same way as it does in other industries, but with an added emphasis on precision and adherence to medical standards. The process begins with a detailed Computer-Aided Design (CAD) model of the medical part. This model is then used to generate Computer-Aided Manufacturing (CAM) programs, which are fed into the CNC machine.
Once the program is loaded, the CNC machine controls the movement of cutting tools or other manufacturing components to create the part. The precision of the CNC machine ensures that each component is manufactured to the exact specifications, ensuring functionality, durability, and safety.
The CNC Machining Process for Medical Devices
-
Design and Modeling: Medical devices and components are first designed using CAD software. The design process involves creating a 3D model that specifies the exact dimensions, features, and tolerances of the part.
-
Program Development: After the design is complete, CAM software is used to generate the machine code or instructions that guide the CNC machine. This code details the cutting paths, tool changes, and other necessary parameters.
-
Material Selection: The appropriate materials for medical devices are selected. CNC machines can handle a wide range of materials commonly used in medical devices, including stainless steel, titanium, ceramics, plastics, and composites.
-
Machining: The CNC machine carries out the machining process based on the CAM program. The machine uses cutting tools to shape, cut, and finish the medical part with high accuracy.
-
Inspection and Quality Control: After machining, the parts are carefully inspected for accuracy, finish, and compliance with medical standards. Quality control ensures that the parts meet the strict regulations required for medical devices.
Benefits of Medical CNC Machining
CNC machining offers several advantages when it comes to the production of medical devices and components. These benefits make it a preferred method in the industry, especially when high precision and repeatability are essential. Some key advantages of medical CNC machining include:
1. High Precision and Accuracy
Medical CNC machining is capable of producing parts with extremely tight tolerancesβoften down to micrometers. This level of precision is essential for medical devices, where even the slightest deviation from the design could have significant consequences. Whether it’s a custom orthopedic implant or a tiny surgical tool, CNC machining ensures that each component fits and functions precisely as intended.
2. Customization
Medical devices often need to be tailored to individual patients or specific needs. CNC machining allows for the production of custom medical components. For example, implants or prosthetics can be designed and manufactured to fit a patientβs unique anatomy. The ability to make custom parts quickly and efficiently is a key advantage in the healthcare sector.
3. Complex Geometries
Many medical devices have intricate designs that would be difficult or impossible to achieve with traditional manufacturing methods. CNC machining can easily handle complex geometries, including fine features like threads, intricate surfaces, and small cavities, making it ideal for the highly detailed nature of medical components.
4. Material Versatility
CNC machines can handle a wide variety of materials commonly used in medical manufacturing. These include biocompatible materials like titanium and stainless steel, as well as advanced polymers, ceramics, and composites. The ability to work with these materials ensures that the medical devices produced are both safe for patients and durable for long-term use.
5. Consistency and Repeatability
Once a CNC program is set up, the machine can produce identical parts with remarkable consistency. This repeatability is vital in the medical field, where large quantities of a particular device may need to be produced without compromising quality or safety.
6. Efficiency and Speed
CNC machining is an automated process, meaning once the machine is programmed and set up, it can operate continuously with minimal operator intervention. This leads to higher productivity and faster turnaround times, making it ideal for manufacturers who need to meet tight deadlines or produce large quantities of medical components.
Applications of Medical CNC Machining
The versatility and precision of CNC machining make it an essential tool in the manufacturing of a wide range of medical products. Here are some of the most common applications of medical CNC machining:
1. Surgical Instruments
Surgical instruments, such as scalpels, forceps, and retractors, must be made with extreme precision to ensure their effectiveness during surgery. CNC machines can create these instruments with exact specifications, ensuring they are sharp, durable, and safe to use in sensitive procedures.
2. Medical Implants
One of the most important applications of CNC machining in the medical field is the production of implants. These include knee replacements, hip implants, dental implants, and more. CNC machines can create implants that perfectly match the patient’s anatomy, which is critical for the success of the implant.
3. Orthopedic Devices
CNC machining is used to manufacture orthopedic devices such as bone plates, screws, and spinal implants. These devices must be durable and able to withstand the stresses placed on them within the human body. CNC technology ensures these devices are crafted to the precise dimensions required for optimal performance.
4. Dental Devices
CNC machining plays a significant role in the dental industry, particularly for the production of dental implants, crowns, bridges, and dentures. CNC machines can work with biocompatible materials to create dental components that are both functional and aesthetically pleasing.
5. Prosthetics
The creation of custom prosthetics, such as artificial limbs, requires a high level of precision and customization. CNC machines can produce prosthetic components tailored to an individual’s measurements and needs, offering patients greater comfort and functionality.
6. Medical Equipment Components
Many medical diagnostic and treatment machines require intricate components that must be manufactured with exacting precision. CNC machining is used to produce parts for machines such as MRI scanners, X-ray machines, ultrasound devices, and more.
The Future of Medical CNC Machining
As technology advances, CNC machining will continue to evolve, offering even greater precision, automation, and customization options for the healthcare industry. The development of multi-axis CNC machines and advancements in 3D printing may open new possibilities for creating highly complex, patient-specific medical devices with even greater speed and efficiency.
Additionally, with the increasing demand for personalized medicine, medical CNC machining will play a central role in producing customized implants, prosthetics, and surgical tools that are designed specifically for individual patients.
Conclusion
Medical CNC machining is a cornerstone of modern healthcare manufacturing. Its precision, efficiency, and ability to handle complex geometries make it an indispensable tool for producing a wide range of medical devices, from implants to surgical instruments. As the healthcare industry continues to advance, the role of CNC technology will become even more critical in ensuring the quality, safety, and effectiveness of medical products.
With its proven benefits and potential for continued innovation, medical CNC machining will remain at the forefront of the healthcare manufacturing process, helping to improve patient outcomes and advance the quality of care worldwide.
Leave a Reply