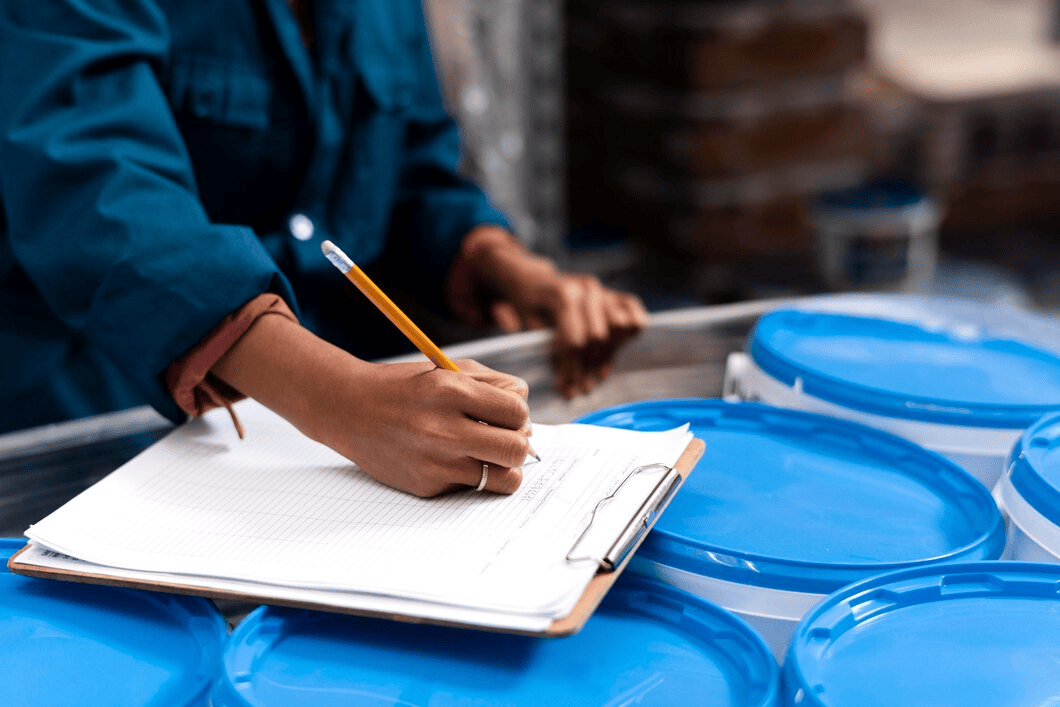
Process validation is a critical component in the pharmaceutical industry. It ensures that a product consistently meets its predetermined specifications and quality standards throughout its lifecycle. With the need to safeguard public health, pharmaceutical manufacturers must adhere to regulatory guidelines set by various agencies. Two prominent regulatory bodies that provide detailed guidance on process validation are the U.S. Food and Drug Administration (FDA) and the European Medicines Agency (EMA).
Both the FDA and EMA have established clear guidelines for process validation, outlining the essential stages that manufacturers must follow. This blog will delve into these stages, compare the guidelines of the FDA and EMA, and help you master regulatory compliance in process validation.
Understanding Process Validation
Process validation is the documented evidence that a process can consistently produce a product that meets its quality specifications. It is fundamental in ensuring that medicines are safe, effective, and high in quality. Process validation involves three distinct stages: Stage 1 (Process Design), Stage 2 (Process Qualification), and Stage 3 (Continued Process Verification).
Although the stages are similar under both FDA and EMA guidelines, there are some key differences in terminology and approach that manufacturers need to be aware of to ensure full compliance.
Stage 1: Process Design
The first stage of process validation focuses on process design. At this stage, the goal is to define the process parameters and performance attributes that will consistently produce a quality product. Both the FDA and EMA stress the importance of thorough research and development (R&D) activities to support process design.
Key activities in Stage 1 include defining critical process parameters (CPPs), identifying quality attributes, and establishing the control strategies needed to maintain consistency. Documentation is crucial, as all data gathered during this phase will support later stages of validation.
The FDA emphasizes scientific risk-based approaches during Stage 1, requiring manufacturers to conduct process development studies and risk assessments. The EMA also encourages a science-based approach, but their focus may involve more detailed documentation to support the processβs overall design.
Stage 2: Process Qualification
Process qualification is the second phase of validation, where the process is evaluated to confirm its reliability and reproducibility under commercial manufacturing conditions. This stage ensures that the manufacturing equipment and processes work as intended, yielding products that meet the predetermined quality standards.
The process qualification stage involves testing and evaluating critical process parameters, quality attributes, and process performance. Manufacturers must collect sufficient data to demonstrate that the process can operate within defined limits.
While both the FDA and EMA require thorough process qualification, the FDA places greater emphasis on statistical analysis and the use of robust data to ensure confidence in the process. The EMA, on the other hand, may focus more on equipment qualification, emphasizing the importance of documenting the performance of each piece of equipment involved in the process.
Stage 3: Continued Process Verification
The final stage of process validation is continued process verification, which is essential for maintaining control over the process throughout the productβs lifecycle. Ongoing monitoring and verification help to identify any changes in the process that could impact product quality.
Continued process verification involves using various tools and techniques to collect real-time data on process performance. This allows manufacturers to detect any deviations and implement corrective actions before product quality is compromised.
Both the FDA and EMA stress the importance of lifecycle management in Stage 3. However, the FDA may place more emphasis on advanced statistical methods and tools for monitoring, while the EMA highlights the importance of regular reviews and reporting on the processβs performance.
Conclusion
In summary, process validation is a critical part of ensuring that pharmaceutical products are safe, effective, and high in quality. Both the FDA and EMA provide clear guidelines for the three stages of process validation: Process Design, Process Qualification, and Continued Process Verification. While the overall goals of both agencies are similar, there are differences in terminology, documentation requirements, and the emphasis placed on certain aspects of the validation process.
Compliance with FDA and EMA guidelines is essential for manufacturers to meet regulatory expectations and maintain product quality throughout its lifecycle. As the pharmaceutical industry continues to evolve, it is likely that process validation guidelines will also adapt, making it crucial for manufacturers to stay informed about any changes in regulatory requirements.
FAQs
What is the purpose of process validation?
Process validation ensures that a manufacturing process consistently produces products that meet quality standards and specifications. It is crucial for maintaining product safety and efficacy.
What are the three stages of process validation?
The three stages are Process Design (Stage 1), Process Qualification (Stage 2), and Continued Process Verification (Stage 3).
How do FDA and EMA guidelines differ?
While both the FDA and EMA aim to ensure product quality, they have different approaches to documentation, risk assessment, and the emphasis placed on certain aspects of process validation. The FDA often focuses more on statistical analysis, while the EMA places greater emphasis on equipment qualification.
What tools are used for continued process verification?
Tools such as statistical process control (SPC), real-time monitoring, and control charts are often used to collect data and verify process performance in Stage 3.
Where can I find more information on FDA and EMA guidelines?
You can visit the official websites of the FDA and EMA for more information on process validation guidelines. For a comprehensive overview, you can also explore resources like MetamorphEduβs courses on regulatory compliance and process validation.
Β
Leave a Reply