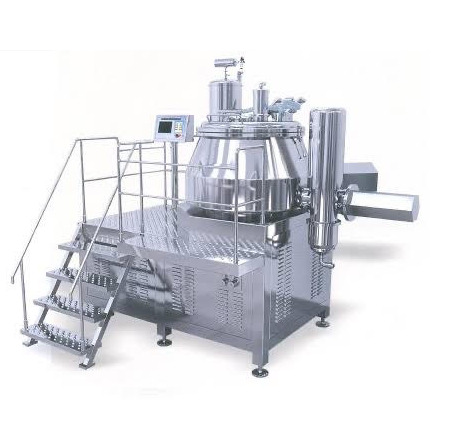
It ensures uniform mixing and granulation of powders, which enhances the quality of final products. However, various factors influence the efficiency and performance of an RMG. Understanding these factors can help optimize operations, reduce production costs, and improve output quality. This article delves into the key parameters affecting the performance of a Rapid Mixer Granulator.
1. Equipment Design and Configuration
1.1 Impeller and Chopper Design
-
The shape, size, and speed of the impeller play a crucial role in mixing and granulation.
-
A well-designed impeller ensures uniform distribution of binder solution and prevents dead zones.
-
The chopper helps in breaking down lumps and controlling particle size distribution.
-
The positioning of the chopper Rapid Mixer Granulator relative to the impeller impacts granule formation and consistency.
1.2 Bowl Geometry and Capacity
-
The shape and size of the mixing bowl influence material movement and granule formation.
-
Overloading or underloading the bowl can lead to inefficient mixing and inconsistent granule size.
-
A properly designed bowl ensures uniform material flow and prevents material buildup.
1.3 Discharge Mechanism
-
A well-functioning discharge port ensures smooth material flow and prevents residual material buildup.
-
Poorly designed discharge valves can lead to clogging and inconsistent granule size.
2. Material Characteristics
2.1 Powder Properties
-
The bulk density, particle size, and moisture content of the raw materials affect granulation.
-
Fine powders require different impeller speeds than coarse powders for effective granulation.
-
Poorly flowing powders can cause uneven mixing, affecting granule uniformity.
2.2 Binder Properties
-
The type and concentration of the binder influence granule strength and flow properties.
-
Low binder concentration leads to weak granules, while excessive binder causes overwetting and large lumps.
-
The viscosity of the binder solution impacts its dispersion and penetration into powder particles.
2.3 Moisture Content
-
The amount of liquid added during granulation affects granule size, strength, and drying requirements.
-
Excess moisture can lead to sticky, large granules, whereas insufficient moisture results in weak granules.
-
Proper moisture control is essential for achieving the desired granule hardness and compressibility.
3. Process Parameters
3.1 Mixing Time and Speed
-
The duration of mixing impacts the homogeneity of the blend and final granule properties.
-
Higher impeller speeds can improve mixing efficiency but may lead to excessive granule attrition.
-
The optimal balance between mixing time and speed ensures consistent granule formation.
3.2 Chopper Speed and Duration
-
The chopper prevents the formation of large lumps and ensures uniform granule size.
-
Excessive chopper speed can lead to excessive fine particles, while low speed results in poor granule formation.
3.3 Liquid Addition Rate and Method
-
The rate of binder addition should be controlled to prevent overwetting or underwetting.
-
Spraying the liquid uniformly enhances distribution and improves granule consistency.
3.4 Temperature Control
-
Heat generated during mixing affects granule properties and drying requirements.
-
Temperature fluctuations can impact binder dispersion and material stability.
-
Cooling systems can help regulate temperature and maintain granule integrity.
4. Environmental Factors
4.1 Humidity and Airflow
-
High humidity levels can affect material flow, granule drying, and product stability.
-
Controlled airflow within the granulator ensures effective moisture removal and prevents lump formation.
4.2 Room Temperature
-
Extreme temperatures can impact the viscosity of the binder and affect granule quality.
-
Consistent temperature control is necessary for reproducible granulation results.
5. Maintenance and Cleaning
5.1 Equipment Calibration and Maintenance
-
Regular maintenance prevents mechanical failures and ensures consistent performance.
-
Worn-out impellers, choppers, or seals can lead to inefficient granulation and material losses.
5.2 Cleaning Procedures
-
Residual material from previous batches can cause cross-contamination and affect product quality.
-
Proper cleaning protocols prevent material buildup and ensure hygiene compliance.
6. Operator Expertise and Training
-
Skilled operators can adjust process parameters effectively for optimal granulation.
-
Training programs ensure staff understand machine operations and troubleshooting.
-
Poor handling can lead to process inefficiencies and inconsistent batch quality.
Conclusion
The performance of a Rapid Mixer Granulator is influenced by multiple factors, including equipment design, material properties, process parameters, environmental conditions, and operator expertise. Optimizing these elements ensures efficient granulation, enhances product quality, and improves overall productivity. Regular monitoring and fine-tuning of these parameters can lead to a more reliable and effective granulation process in pharmaceutical and industrial applications.
Β
Leave a Reply