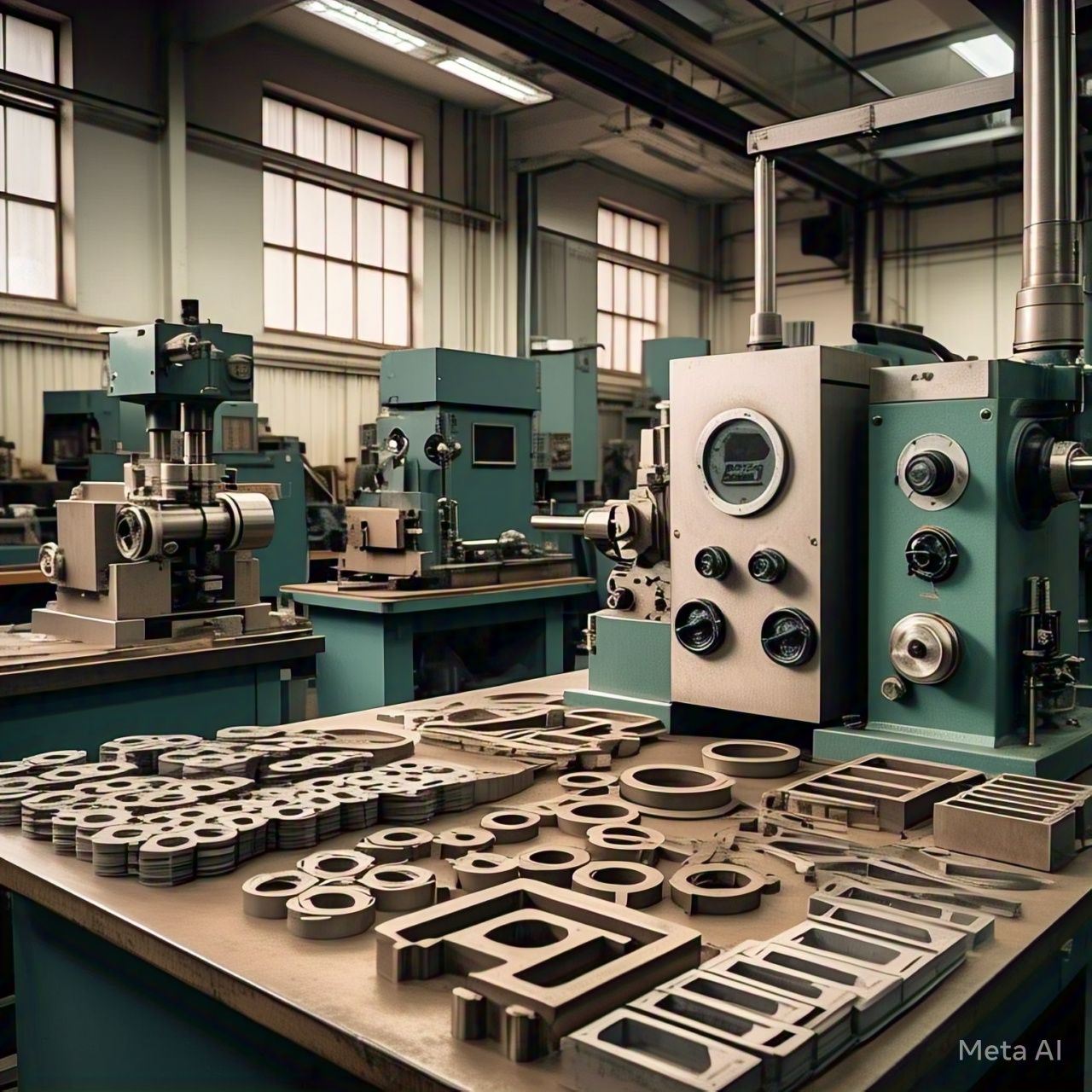
Gaskets play a crucial role in various industries, ensuring sealing, insulation, and protection in mechanical and industrial applications. Custom gasket manufacturing allows businesses to create tailor-made gaskets that fit unique requirements, improving efficiency and reducing risks such as leaks and contamination.
From automotive engines to aerospace components, medical devices, and industrial machinery, precision-made gaskets ensure optimal performance, durability, and safety. In this guide, we’ll explore custom gasket manufacturing, materials, production methods, benefits, and how to choose the right manufacturer.
What is Custom Gasket Manufacturing?
Definition
Custom gasket manufacturing is the process of designing and producing gaskets based on specific customer requirements. These gaskets are used to seal joints, prevent leakage, reduce vibration, and protect equipment from environmental damage.
Why Use Custom Gaskets Instead of Standard Ones?
- Perfect Fit: Designed specifically for your application, ensuring seamless sealing.
- Enhanced Durability: Made from specialized materials suited to temperature, pressure, and chemical exposure conditions.
- Improved Efficiency: Reduces downtime, maintenance, and energy loss.
- Industry Compliance: Meets specific safety and performance standards required in critical industries.
Common Materials Used in Custom Gaskets
1. Rubber Gaskets
- Neoprene: Good for oil and fuel resistance.
- Silicone: Ideal for high-temperature applications.
- EPDM (Ethylene Propylene Diene Monomer): Excellent weather and UV resistance.
2. Metal Gaskets
- Stainless Steel: High strength and corrosion resistance.
- Copper: Great for thermal conductivity.
- Aluminum: Lightweight and durable.
3. Composite & Fiber Gaskets
- Graphite Gaskets: Excellent for high heat and pressure environments.
- PTFE (Teflon) Gaskets: Resistant to chemicals and extreme temperatures.
- Cork Gaskets: Used in low-pressure sealing applications.
4. Foam & Felt Gaskets
- Polyurethane Foam: Ideal for shock absorption and insulation.
- Felt Gaskets: Used for filtration and cushioning.
Custom Gasket Manufacturing Processes
1. Die Cutting
- Uses steel rule dies to stamp out gaskets from a sheet material.
- Suitable for high-volume production.
2. CNC Gasket Cutting
- Computer-controlled cutting for precision and complex designs.
- Ideal for low-volume or prototype gaskets.
3. Waterjet Cutting
- Uses high-pressure water to cut materials without heat.
- Perfect for thick or heat-sensitive materials.
4. Injection Molding
- Liquid material is injected into molds to create custom shapes.
- Used for rubber and plastic gaskets.
5. Compression Molding
- Material is compressed under heat and pressure into a specific shape.
- Common for rubber gaskets.
6. Laser Cutting
- Provides extreme accuracy for small, intricate designs.
- Ideal for medical and electronics applications.
Industries That Use Custom Gaskets
1. Automotive & Transportation
- Engine seals, fuel systems, and transmission components.
- Vibration-dampening gaskets for electric vehicles (EVs).
2. Aerospace & Defense
- Sealing components in aircraft engines and fuel systems.
- High-temperature gaskets for jet turbines.
3. Medical & Pharmaceutical
- Sterile gaskets for medical devices.
- Seals for chemical-resistant lab equipment.
4. Oil & Gas Industry
- Gaskets for pipelines, pumps, and valves.
- Heat-resistant seals for high-pressure applications.
5. Industrial Machinery & HVAC Systems
- Gaskets for compressors, heat exchangers, and refrigeration units.
- Seals to prevent air or gas leaks in HVAC ducts.
Leading Manufacturing Solutions
Leading manufacturing solutions focus on innovation, efficiency, and precision to meet industry demands. By utilizing advanced technology and high-quality materials, manufacturers enhance production processes, reduce costs, and ensure superior product performance. These solutions cater to various industries, including automotive, aerospace, and construction, driving growth and reliabi lity in modern manufacturing.
Benefits of Custom Gasket Manufacturing
1. Precision Engineering & Fit
Custom gaskets are tailored to exact specifications, ensuring a perfect seal and minimizing leakage risks.
2. High Performance & Durability
Made from top-quality materials, custom gaskets offer longer lifespan and resistance to extreme conditions.
3. Reduced Downtime & Maintenance Costs
By eliminating leaks and equipment failures, custom gaskets help businesses reduce costly repairs and replacements.
4. Improved Safety & Compliance
Custom gaskets meet industry safety regulations, ensuring proper insulation, chemical resistance, and environmental protection.
5. Compatibility with Specialized Equipment
Many industrial applications require unique gasket shapes and materials, which standard gaskets cannot provide.
How to Choose the Right Custom Gasket Manufacturer
1. Industry Experience & Reputation
Look for manufacturers with a strong track record in your industry, such as automotive, aerospace, or oil and gas.
2. Material Expertise
Ensure the manufacturer offers a wide selection of materials, including rubber, metal, and high-performance composites.
3. Customization Capabilities
A good manufacturer should provide CNC cutting, molding, and die-cutting services to meet specific design requirements.
4. Quality Certifications & Standards
Check if the manufacturer complies with industry certifications like:
- ISO 9001 (Quality Management)
- ASTM Standards (Material Testing)
- FDA Compliance (Medical-Grade Gaskets)
5. Lead Times & Production Capacity
Make sure they can meet your delivery deadlines and scale production based on demand.
6. Customer Support & Engineering Assistance
A reliable manufacturer provides design consultation, prototyping, and technical support to optimize gasket performance.
Future Trends in Custom Gasket Manufacturing
1. Smart & Sensor-Integrated Gaskets
Gaskets with embedded sensors can monitor pressure, leaks, and performance in real time.
2. Sustainable & Recyclable Gasket Materials
Eco-friendly materials like biodegradable rubber and recycled composites are becoming more popular.
3. 3D Printing for Rapid Prototyping
3D-printed gaskets allow for faster prototyping and complex geometries without tooling costs.
4. High-Temperature & Chemical-Resistant Innovations
Advanced materials are being developed to withstand extreme environments in aerospace, chemical processing, and energy industries.
Conclusion
Custom gasket manufacturing is essential for industries requiring precision sealing solutions tailored to specific applications. Whether you need gaskets for automotive engines, medical devices, aerospace components, or industrial machinery, choosing the right materials and manufacturing process is crucial for performance and durability.
Metal shim manufacturing involves producing thin, precision-cut metal pieces used for alignment, spacing, and support in various industrial applications.By working with a trusted custom gasket manufacturer, businesses can ensure optimal sealing, reduced maintenance, and compliance with industry standards
FAQs
1. What is the difference between standard and custom gaskets?
Standard gaskets are pre-made with fixed dimensions, while custom gaskets are designed for specific applications, ensuring a perfect fit and better performance.
2. What materials are best for high-temperature gaskets?
Graphite, silicone, PTFE, and metal gaskets are excellent for high-heat applications such as engines and turbines.
3. Can custom gaskets be made in small quantities?
Yes, many manufacturers offer low-volume production or prototypes for specialized applications.
4. What is the lifespan of a custom gasket?
Lifespan depends on material, usage, and environmental conditions, but high-quality gaskets can last several years with proper maintenance.
5. How do I ensure my gasket meets industry regulations?
Choose a manufacturer with ISO 9001, ASTM, or FDA certifications to guarantee compliance.
6. Can custom gaskets be used for food and medical applications?
Yes, FDA-approved materials like PTFE and medical-grade silicone are used in these industries.
7. What is the best manufacturing method for complex gasket designs?
CNC cutting, waterjet cutting, and 3D printing are ideal for intricate and high-precision gaskets.
8. How thick can a custom gasket be?
Thickness varies based on application, typically ranging from 0.5mm to 10mm or more.
9. What industries benefit most from custom gaskets?
Automotive, aerospace, oil & gas, medical, HVAC, and industrial machinery.
10. How can I get a custom gasket quote?
Contact a manufacturer with your design specs, material preferences, and quantity needed for a detailed quote.
Leave a Reply