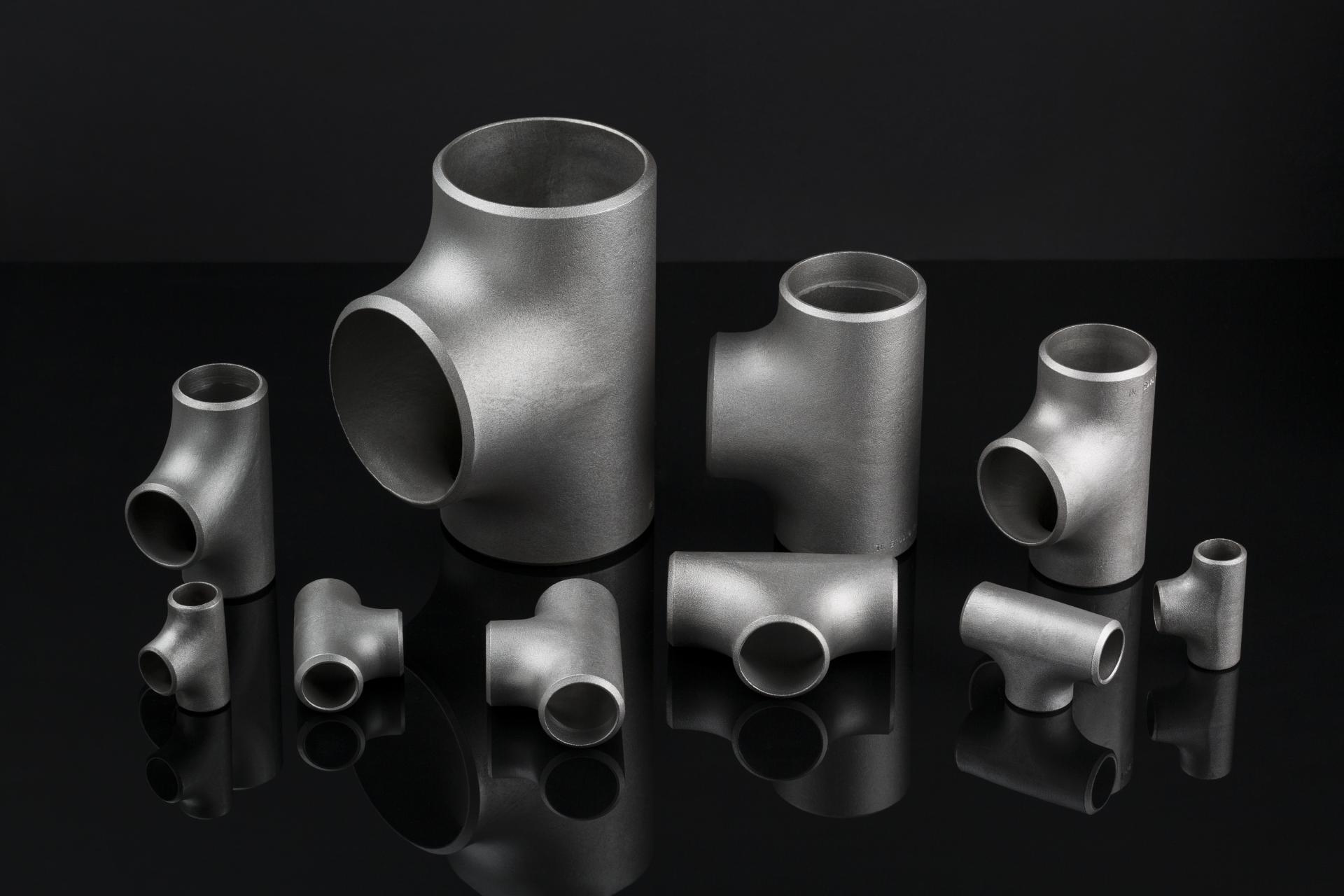
In the realm of industrial piping, where corrosive environments reign supreme, standard materials often falter. This is where specialized alloys step in, offering exceptional resistance and longevity. Among these, Alloy 20 forged fittings stand out as a premier solution for handling aggressive chemicals and extreme conditions.
But what makes Alloy 20 so unique, and why are forged fittings crafted from this material so critical? Let’s delve into the properties and applications that make these fittings essential in demanding industries.
Alloy 20: A Fortress Against Corrosion
Alloy 20, also known as Carpenter 20, is a nickel-iron-chromium austenitic alloy specifically designed for superior corrosion resistance. It boasts a complex chemical composition, including molybdenum and copper, which work synergistically to provide exceptional protection against a wide range of corrosive media, particularly sulfuric acid.
This alloy’s resistance extends beyond sulfuric acid, encompassing other aggressive chemicals like nitric acid, chloride solutions, and various organic acids. This makes it an ideal choice for applications where standard stainless steels would quickly succumb to corrosion.
The Forging Advantage: Enhancing Performance
The forging process amplifies the inherent corrosion resistance of Alloy 20 by refining its grain structure and eliminating internal defects. This results in fittings that are not only highly resistant to corrosion but also possess enhanced mechanical strength and durability.
Forged fittings, unlike cast fittings, are produced through a process of shaping heated metal using compressive forces. This process creates a dense, uniform structure that significantly improves the material’s resistance to cracking, fatigue, and impact. This is crucial in applications where high pressures, temperatures, and mechanical stresses are combined with corrosive environments.
Key Benefits of Alloy 20 Forged Fittings:
- Exceptional Corrosion Resistance: Superior resistance to sulfuric acid and a wide range of other aggressive chemicals.
- Enhanced Mechanical Strength: The forging process improves the material’s strength, toughness, and durability.
- Long Service Life: Alloy 20’s resistance to corrosion and mechanical degradation ensures a long service life, reducing maintenance and replacement costs.
- Reliability in Extreme Conditions: Suitable for applications involving high pressures, temperatures, and corrosive environments.
- Versatility: Available in various configurations, including elbows, tees, couplings, and reducers, to meet diverse piping requirements.
Applications in Critical Industries:
The unique properties of Alloy 20 forged fittings make them essential in various industries where corrosion resistance is paramount:
- Chemical Processing: Handling sulfuric acid, nitric acid, and other aggressive chemicals in production and storage.
- Petrochemical: Processing and transporting corrosive fluids and gases in refineries and chemical plants.
- Pharmaceutical: Manufacturing and handling corrosive chemicals and intermediates in pharmaceutical production.
- Food Processing: Handling corrosive cleaning agents and processing fluids in food and beverage production.
- Pollution Control: Managing corrosive effluents and gases in pollution control systems.
- Desalination: Handling highly corrosive seawater and brine in desalination plants.
Selecting and Maintaining Alloy 20 Forged Fittings:
When choosing Alloy 20 forged fittings, it’s crucial to consider the following factors:
- Chemical Composition: Ensure the alloy’s composition meets the specific requirements of the application.
- Pressure and Temperature Ratings: Verify that the fittings can withstand the operating conditions of the piping system.
- Standards and Specifications: Confirm that the fittings comply with relevant industry standards, such as ASTM and ASME.
- Manufacturer Reputation: Choose a reputable manufacturer with experience in producing high-quality Alloy 20 fittings.
Regular inspection and maintenance are essential for ensuring the continued reliability of these fittings. This includes visual inspections for signs of corrosion, damage, or leaks, as well as periodic pressure testing.
In conclusion, Alloy 20 forged fittings provide a robust and reliable solution for handling corrosive environments. Their exceptional corrosion resistance, combined with the enhanced mechanical properties achieved through forging, makes them indispensable in critical industrial applications. By understanding their properties and applications, engineers and technicians can ensure the long-term integrity and safety of their piping systems.
Leave a Reply