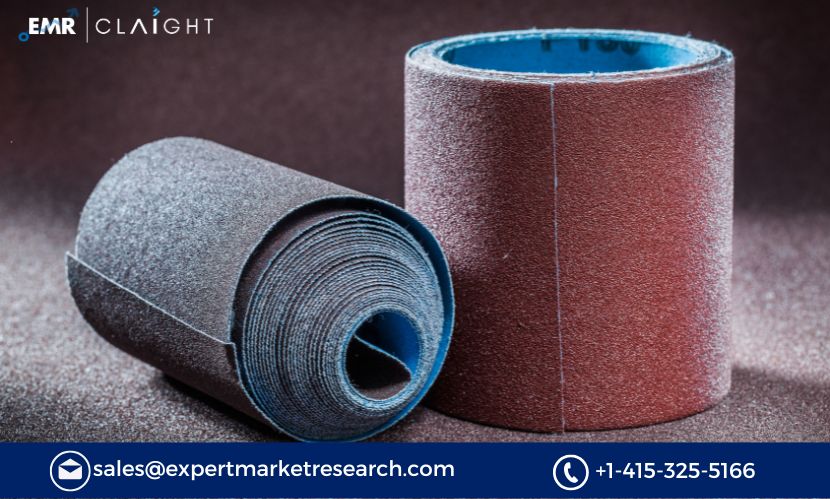
Introduction
Abrasive paper, also known as sandpaper or sanding paper, is a versatile material commonly used in the manufacturing and finishing of products in various industries. The primary function of abrasive paper is to smooth surfaces by grinding, polishing, or cleaning materials like wood, metal, plastic, and other substrates. The increasing demand for high-quality finishes in industries such as automotive, furniture, construction, and metalworking has made abrasive paper a vital material. As technology advances, so does the demand for improved abrasives with better durability, performance, and efficiency. For entrepreneurs looking to enter the manufacturing sector, setting up an abrasive paper manufacturing plant can be a profitable business venture. This abrasive paper manufacturing plant project report outlines the essential components involved in establishing a successful manufacturing facility, including the market potential, raw materials, production processes, equipment, and financial projections.
Market Overview and Growth Prospects
The global market for abrasive paper is expanding due to the growing demand for polished, smooth, and fine finishes in various industries. As more industries adopt advanced manufacturing techniques, the requirement for high-quality abrasives that can deliver precise finishes has increased. Additionally, the rise in DIY (Do-It-Yourself) home improvement projects and the growing automotive and furniture sectors are contributing to the demand for abrasive paper.
Key drivers of the abrasive paper market include:
- Increased Demand in the Automotive Sector: The automotive industry requires abrasive materials for various applications, including bodywork, paint removal, surface preparation, and polishing. Abrasive paper is widely used in automotive manufacturing and repair.
- Construction and Furniture Manufacturing: The growing construction industry and the demand for fine finishes in furniture production also drive the demand for abrasive papers, especially for sanding wood, drywall, and metal surfaces.
- Rising DIY Culture: With an increasing number of consumers engaged in DIY projects, especially in home renovations and repairs, the demand for affordable, easy-to-use abrasive papers has surged.
- Technological Advancements: Innovations in abrasive materials, such as the development of coated abrasive papers with better performance and longer lifespan, are expected to drive market growth.
The expanding demand for abrasives, combined with improvements in production technology, presents significant opportunities for the establishment of abrasive paper manufacturing plants.
Get a Free Sample Report with Table of Contents@
Key Components of an Abrasive Paper Manufacturing Plant
Setting up an abrasive paper manufacturing plant requires a deep understanding of the raw materials, production process, equipment, and infrastructure needed to produce high-quality abrasive paper. Below are the key components involved in the establishment of an abrasive paper manufacturing facility.
1. Raw Materials and Ingredients
The raw materials used in the production of abrasive paper are crucial to achieving the desired performance and durability of the finished product. The primary raw materials include:
- Backing Material: The backing material is the base onto which the abrasive grains are coated. Common backing materials for abrasive paper include paper, cloth, polyester, and fiberglass. Paper is the most commonly used backing material due to its low cost and ease of use.
- Abrasive Grains: These are the particles responsible for the abrasive action. The most common abrasive materials used in the production of abrasive paper are aluminum oxide, silicon carbide, garnet, and emery. Aluminum oxide is widely used due to its durability and versatility, while silicon carbide is preferred for fine finishes and harder materials.
- Bonding Agents: Bonding agents are used to attach the abrasive grains to the backing material. These agents include resins, glues, and adhesives that hold the abrasive particles in place and enhance the durability of the abrasive paper.
- Coating Materials: Some abrasive papers may be coated with additional materials like stearate, which helps reduce clogging and improves the performance of the paper.
The quality and consistency of the raw materials are critical for ensuring that the final abrasive paper performs effectively and lasts longer.
2. Manufacturing Process
The manufacturing process of abrasive paper involves several key stages, each of which is important for creating high-quality, durable products. Below is an outline of the typical steps involved in the production of abrasive paper:
Step 1: Preparing the Backing Material
The first step in the manufacturing process is preparing the backing material. The paper or cloth backing is sourced in large rolls and cut to the required size for production. The backing material is then cleaned and pre-treated to ensure that it adheres to the abrasive grains.
Step 2: Coating the Backing Material
Once the backing material is prepared, it is coated with an adhesive or bonding agent that will hold the abrasive grains in place. The adhesive is typically applied in a thin layer on the surface of the backing material using rollers or a spraying process. This process is done in a controlled environment to ensure that the coating is uniform and free of defects.
Step 3: Applying the Abrasive Grains
Next, the abrasive grains are evenly spread or sprinkled onto the coated backing material. The grains are typically applied using a mechanical process, such as spraying or rolling, ensuring that they are evenly distributed across the surface. The type of abrasive grain selected for the paper depends on the application and desired finish.
Step 4: Curing and Drying
After the abrasive grains are applied, the adhesive must be cured to set the grains in place. The curing process is typically done by heating the material in an oven or drying chamber. This step ensures that the adhesive bonds securely to both the abrasive grains and the backing material, resulting in a durable and long-lasting product.
Step 5: Finishing and Cutting
Once the paper is fully dried and cured, it undergoes finishing processes such as trimming and cutting to the desired size. Depending on the product specifications, the abrasive paper may be cut into sheets, rolls, or discs, which are then packaged for distribution.
Step 6: Quality Control
Throughout the production process, quality control measures are essential to ensure that the abrasive paper meets the required standards for durability, abrasiveness, and consistency. Testing is conducted at various stages to check for defects, such as uneven coatings, loose abrasive particles, or poor bonding. The final product is tested for performance in real-world applications.
3. Manufacturing Equipment
The production of abrasive paper requires specialized equipment designed for precision and efficiency. The key machinery and equipment used in the manufacturing process include:
- Coating Machines: These machines apply the adhesive or bonding agent to the backing material. Rollers or sprayers are used to ensure an even application of the coating.
- Grain Spreading Machines: These machines are used to spread and apply abrasive grains evenly onto the coated backing material.
- Curing Ovens: Curing ovens are used to dry and set the adhesive, ensuring that the abrasive grains are securely bonded to the backing material.
- Slitters and Cutters: These machines are used to cut the finished abrasive paper into various sizes, such as sheets, discs, or rolls.
- Quality Control Equipment: Testing machines for measuring the abrasive performance, adhesion strength, and durability of the final product.
Choosing the right equipment is critical for ensuring efficient production and high-quality products.
4. Plant Layout and Design
The layout and design of the abrasive paper manufacturing plant play a significant role in maximizing production efficiency and minimizing waste. Key considerations for plant layout include:
- Raw Material Storage: Adequate space should be allocated for storing raw materials such as backing paper, abrasive grains, and bonding agents.
- Production Line Setup: The plant should be designed with a streamlined production line to facilitate the smooth flow of materials from one stage to the next, minimizing delays and material handling.
- Quality Control and Testing Area: A dedicated area for inspecting and testing the quality of the finished abrasive paper should be included in the layout.
- Storage and Packaging Area: After the abrasive paper is cut, it should be stored in a clean, dry area before being packaged for distribution.
- Safety Considerations: Safety measures such as fire protection, ventilation, and appropriate PPE (Personal Protective Equipment) should be included in the plant design to protect workers.
5. Regulatory Requirements and Compliance
Abrasive paper manufacturing plants must comply with several regulatory requirements to ensure product safety and environmental sustainability. These include:
- Occupational Health and Safety Regulations: The plant must adhere to local health and safety regulations to protect workers from exposure to hazardous materials, machinery accidents, and other risks.
- Environmental Regulations: The manufacturing process should comply with environmental standards regarding waste disposal, air quality, and the use of chemicals to minimize the plantβs environmental impact.
- Product Standards: Abrasive papers must meet industry standards for quality and performance, such as those set by national and international bodies.
6. Financial Projections and Investment Considerations
Starting an abrasive paper manufacturing plant requires a considerable financial investment. Some key financial factors to consider include:
- Initial Investment: The cost of land, plant construction, equipment procurement, and raw material acquisition.
- Operating Costs: Ongoing expenses such as labor, utilities, raw materials, packaging, and maintenance.
- Revenue Generation: The revenue potential depends on production capacity, pricing strategies, and market demand for abrasive paper.
- Return on Investment (ROI): Financial projections should include ROI, break-even analysis, and long-term profitability.
Media Contact
Company Name: Claight Corporation
Contact Person: Lewis Fernandas, Corporate Sales Specialist β U.S.A.
Email: sales@expertmarketresearch.com
Toll Free Number: +1β415β325β5166 | +44β702β402β5790
Address: 30 North Gould Street, Sheridan, WY 82801, USA
Website: www.expertmarketresearch.com
Aus Site: https://www.expertmarketresearch.com.au
Leave a Reply