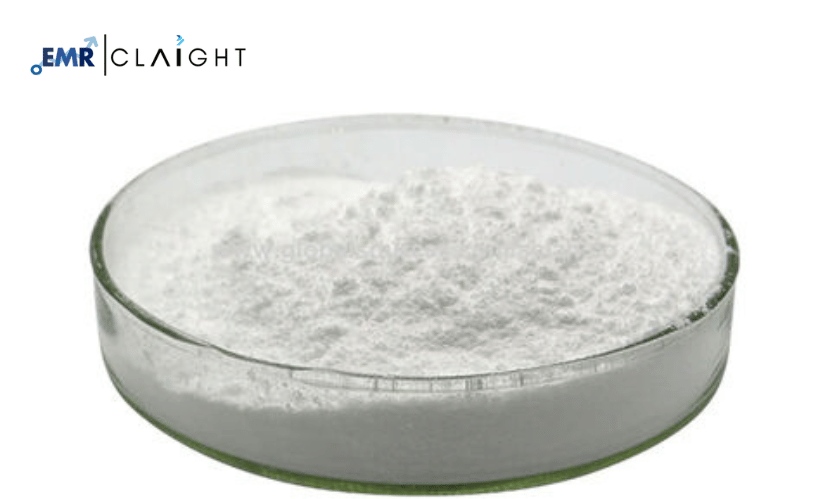
Magnesium antimonate, a unique compound with exceptional flame-retardant properties, plays a significant role in industries such as electronics, plastics, and coatings. Its thermal stability and ability to enhance fire resistance make it an essential additive in various high-performance applications. Establishing a magnesium antimonate manufacturing plant requires advanced technology, strict quality control, and adherence to environmental regulations. This article provides a comprehensive guide to the production process, required equipment, and critical considerations for launching a successful magnesium antimonate manufacturing facility.
Understanding Magnesium Antimonate
Magnesium antimonate is an inorganic compound typically used as a flame retardant additive. It is valued for its ability to enhance the safety and durability of materials by improving their resistance to heat and combustion. Applications of magnesium antimonate span across industries, making it a critical material for specialised products.
Get a Free Sample Report with Table of Contents@ https://www.expertmarketresearch.com/prefeasibility-reports/magnesium-antimonate-manufacturing-plant-project-report/requestsample
Key Processes in Manufacturing
- Raw Material Preparation
- The production of magnesium antimonate begins with sourcing high-purity magnesium and antimony compounds. These raw materials undergo quality checks to ensure compatibility and consistency.
- Reaction Process
- Magnesium and antimony compounds are subjected to a controlled reaction under high temperatures. Specific parameters such as pressure, temperature, and reaction time are carefully monitored to achieve optimal yield and quality.
- Filtration and Purification
- The reaction mixture is filtered to remove impurities. Purification techniques such as washing or chemical treatment may be employed to enhance the productโs quality.
- Drying and Granulation
- The filtered magnesium antimonate is dried to remove moisture and processed into granules or powder, depending on the intended application.
- Quality Testing
- The final product undergoes rigorous testing to verify its thermal stability, particle size, and flame-retardant properties.
- Packaging and Storage
- The product is securely packaged in chemical-grade containers and stored under controlled conditions to maintain its integrity during transportation and storage.
Essential Equipment for a Manufacturing Plant
Setting up a magnesium antimonate manufacturing plant requires advanced machinery and technology to ensure safe and efficient production. Key equipment includes:
- Reactors: For carrying out high-temperature reactions under controlled conditions.
- Filtration Systems: To separate impurities from the reaction mixture.
- Drying Units: For removing moisture and preparing the product for final processing.
- Granulators: To produce uniform granules for industrial applications.
- Quality Testing Instruments: For analysing thermal stability, particle size, and other critical properties.
- Packaging Machines: For securely sealing and labelling the finished product.
Designing the Plant Layout
An efficient plant layout is crucial for optimising operations and meeting safety standards. Key considerations include:
- Raw Material Storage: Secure areas for storing magnesium and antimony compounds.
- Processing Zones: Dedicated sections for reaction, filtration, drying, and granulation.
- Quality Control Laboratory: Equipped for testing raw materials and finished products.
- Packaging and Storage Areas: Facilities for sealing and storing the final product.
- Waste Management Systems: For handling and disposing of by-products responsibly.
Quality Control in Manufacturing
Ensuring consistent quality is critical for magnesium antimonate production. Key quality control practices include:
- Raw Material Testing: Verifying the purity and compatibility of magnesium and antimony compounds.
- Process Monitoring: Ensuring optimal reaction conditions for efficiency and product consistency.
- Product Testing: Assessing flame-retardant properties, particle size, and thermal stability.
- Packaging Inspection: Checking for secure seals and accurate labelling on containers.
Regulatory and Licensing Requirements
Establishing a magnesium antimonate manufacturing plant involves compliance with various industrial and environmental standards. Key requirements include:
- Chemical Safety Certifications: Adherence to regulations for handling and storing hazardous materials.
- Environmental Clearances: Managing emissions, waste, and effluents responsibly.
- Labelling Compliance: Providing accurate product information and safety precautions.
- Workplace Safety Regulations: Ensuring worker safety through training and proper handling protocols.
Applications of Magnesium Antimonate
Magnesium antimonate is widely used in various industries due to its flame-retardant and thermal properties:
- Electronics: Incorporated into components to improve fire resistance in devices and circuits.
- Plastics: Used as a flame-retardant additive in thermoplastics and thermosetting polymers.
- Coatings: Applied in fire-resistant paints and industrial coatings.
- Advanced Materials: Used in the development of composite materials for high-performance applications.
- Research and Development: Valued in specialised studies for creating innovative products.
Sustainability in Manufacturing
Sustainability plays a vital role in magnesium antimonate production. Key measures to enhance sustainability include:
- Eco-Friendly Processes: Using efficient reaction techniques to minimise waste and emissions.
- Waste Recycling: Repurposing by-products for secondary applications.
- Emission Control: Implementing scrubbers and advanced filtration systems to reduce environmental impact.
- Energy Efficiency: Adopting energy-saving technologies in reactors and drying units.
Market Trends and Opportunities
The magnesium antimonate market is experiencing growth due to its critical role in flame-retardant applications and rising safety standards. Key trends include:
- Increasing Demand in Electronics: Rising production of fire-resistant components in consumer and industrial electronics.
- Growth in Construction Materials: Increased use in coatings and materials for fireproof buildings.
- Global Expansion: Growing adoption in emerging markets driven by industrialisation and infrastructure development.
- Focus on Sustainability: Development of eco-friendly flame-retardant solutions to meet regulatory and consumer demands.
Challenges in the industry include:
- Raw Material Costs: Managing fluctuations in magnesium and antimony compound prices.
- Regulatory Compliance: Navigating complex environmental and safety standards.
- Market Competition: Differentiating products through innovation and consistent quality.
By implementing advanced production techniques, ensuring stringent quality control, and prioritising sustainability, manufacturers can establish a successful magnesium antimonate production facility to cater to the growing global demand across diverse industries.
Leave a Reply