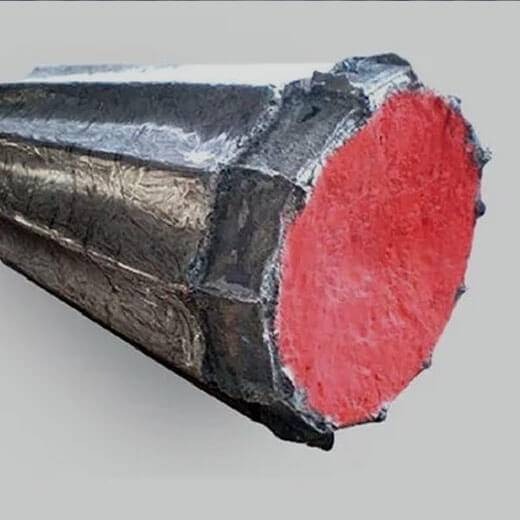
Forging quality ingots are the backbone of numerous industrial processes, serving as the raw material for creating high-strength, durable components. Whether you’re a manufacturer, engineer, or someone exploring the world of metallurgy, understanding the importance of forging quality ingots is crucial. In this article, we’ll dive deep into the key features, industrial applications, and why choosing the right Supplier of Forging Quality Ingots can make all the difference.
What Are Forging Quality Ingots?
Forging Quality Ingots are semi-finished metal products, typically made from steel, aluminum, or other alloys, that are specifically designed for forging processes. These ingots are cast into shapes that allow them to be further processed under high pressure and temperature to create components with superior mechanical properties.
The term forging quality implies that these ingots meet stringent standards in terms of chemical composition, internal structure, and surface quality. This ensures they can withstand the rigors of forging without developing defects like cracks or inclusions.
Key Features of Forging Quality Ingots
When selecting Forging Quality Ingots, certain features are non-negotiable. Here’s what sets them apart:
1. High Purity and Consistent Composition
The chemical composition of forging quality ingots is carefully controlled to ensure uniformity. Impurities are minimized to prevent weaknesses in the final forged product. For example, steel ingots often have controlled levels of carbon, manganese, and other alloying elements to achieve desired properties like hardness and tensile strength.
2. Superior Internal Structure
The internal structure of forging quality ingots is free from defects such as porosity, shrinkage cavities, or segregation. This is achieved through advanced casting techniques and rigorous quality checks.
3. Excellent Surface Finish
A smooth, defect-free surface is essential to avoid cracks or imperfections during forging. Suppliers often machine or grind the surfaces of ingots to meet these standards.
4. Dimensional Accuracy
Forging Quality Ingots are produced with precise dimensions to ensure they fit seamlessly into forging equipment. This reduces material waste and improves efficiency.
5. Thermal and Mechanical Properties
These ingots are designed to withstand extreme temperatures and pressures during forging. Their thermal conductivity and mechanical strength are tailored to specific industrial needs.
Industrial Applications of Forging Quality Ingots
Forging Quality Ingots are indispensable in a wide range of industries. Their ability to be shaped into high-performance components makes them a preferred choice for critical applications.
1. Aerospace Industry
In aerospace, components must withstand extreme conditions, including high stress and temperature variations. Forging quality ingots are used to produce turbine blades, landing gear, and other critical parts that require exceptional strength and durability.
2. Automotive Industry
From engine components to transmission parts, forging quality ingots are the foundation of many automotive parts. Their high strength-to-weight ratio makes them ideal for improving fuel efficiency and performance.
3. Oil and Gas Sector
The oil and gas industry relies on forging quality ingots to create drill bits, valves, and pipelines that can endure harsh environments, including high pressure and corrosive substances.
4. Power Generation
In power plants, forging quality ingots are used to manufacture turbine shafts, generator rotors, and other components that operate under high stress and temperature.
5. Heavy Machinery
Construction and mining equipment often require parts that can handle heavy loads and abrasive conditions. Forging quality ingots provide the necessary strength and wear resistance.
Why Choosing the Right Supplier of Forging Quality Ingots Matters
The quality of your forged components depends heavily on the quality of the ingots you start with. Here’s why partnering with a reliable Supplier of Forging Quality Ingots is critical:
1. Consistency in Quality
A reputable supplier ensures that every batch of ingots meets the same high standards, reducing the risk of defects in your final products.
2. Customization Options
Different applications require different specifications. A trusted supplier can provide ingots tailored to your unique needs, whether it’s a specific alloy or dimensional requirement.
3. Technical Expertise
Experienced suppliers offer valuable insights into material selection, helping you choose the right ingots for your application.
4. Timely Delivery
In industries where downtime is costly, a reliable supplier ensures that you receive your ingots on time, every time.
5. Competitive Pricing
While quality is paramount, cost-effectiveness is also important. A good supplier strikes the right balance between quality and affordability.
Conclusion
Forging Quality Ingots are the foundation of countless industrial applications, from aerospace to heavy machinery. Their superior features, including high purity, excellent internal structure, and precise dimensions, make them indispensable for producing high-performance components.
Choosing the right Supplier of Forging Quality Ingots is equally important. A reliable supplier ensures consistency, customization, and timely delivery, helping you achieve the best results in your forging processes.
Whether you’re new to the world of forging or a seasoned professional, understanding the importance of forging quality ingots can help you make informed decisions and drive success in your projects.
Leave a Reply