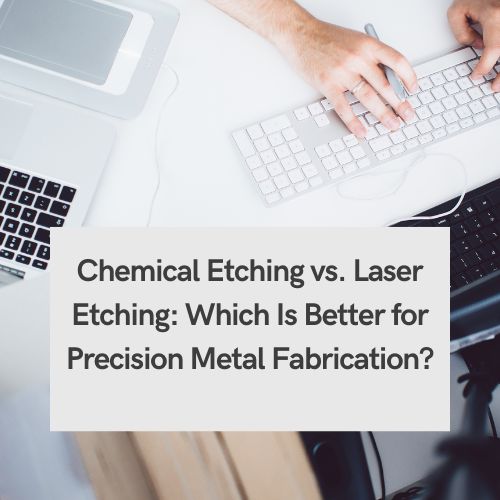
During precision metal fabrication, manufacturers turn to various etching methods in an effort to cut intricate patterns, markings, and designs onto the surface of the metal. Some of the more popular approaches to etching involve chemical etching and laser etching. While each one comes with pros and cons, project specifications would demand that they both be compared with a view toward selecting the correct method to meet the necessary goals. In the following article, we will contrast chemical etching and laser etching to assist you in choosing the best method for your application.
What Is Chemical Etching?
Chemical etching, or chemical milling and photochemical machining (PCM), is a subtractive manufacturing method that employs chemical solutions to dissolve non-desired metal parts selectively. The process is a case of applying a photoresist mask to the surface of the metal, exposing desired areas to the etching solution, and subsequently removing the mask to expose the final pattern.
Advantages of Chemical Etching
- High Precision and Detail: With chemical etching, it’s possible to make very fine and detailed designs and have tolerances as close as Β±0.025 mm.
- No Mechanical Stress: Since etching chemically doesn’t stress the material with force like machinery does, neither warping nor distortion is present.
- Cost-Effective for Large Batches: After preparing the masking setup, mass production would be extremely affordable compared to all other methods.
- Ideal for Thin and Delicate Metals: It is best used for thin metal sheets since there is no heat-affected zone (HAZ).
- Versatile with Different Metals: It can etch stainless steel, aluminum, copper, brass, and even some unusual metals.
Advantages and Disadvantages of Chemical Etching
- Time-Consuming Process: It is a multi-step process that involves mask preparation and chemical treatment, which can be time-consuming compared to laser etching.
- Hazardous Chemicals: Handling acids and other chemicals is environmentally and safety hazardous.
- Limited Depth Control: Chemical etching strips away material evenly, but variable depths are difficult to obtain.
What Is Laser Etching?
Laser etching is a subtractive process that employs a high-intensity laser beam to vaporize the metal surface, leaving behind permanent marks. The process is commonly applied to engrave serial numbers, barcodes, logos, and intricate designs.
Advantages of Laser Etching
- Fast and Accurate: Laser etching achieves high-speed marking with micron-level accuracy.
- No Chemicals Involved: Contrary to chemical etching, it is an environmentally friendly process with no toxic chemicals involved.
- Flexible Depth Control: Etching depth can be readily controlled by adjusting laser power and frequency.
- Best for Prototyping and Small Runs: As no masks and templates are required, laser etching is ideal for rapid prototyping and small-run custom work.
- Operates on a Broad Variety of Materials: Laser etching is applicable on metals such as stainless steel, titanium, and aluminum, as well as ceramics and plastics.
Drawbacks of Laser Etching
- Heat-Affected Zone (HAZ): Laser creates heat, which affects the material by causing color changes, warping, or changes in its properties.
- Increased Equipment Costs: The cost of purchasing laser equipment is high in comparison to that of chemical etching equipment.
- Not Suitable for Thin Metals: Thin metal sheets are damaged by high-intensity laser beams, and hence chemical etching would be more suitable for the purpose.
Comparison: Chemical Etching vs. Laser Etching
Chemical etching is highly precise and best suited for complex designs, especially on thin metals, because it does not introduce any mechanical stress or heat damage. But it is slower and uses dangerous chemicals. On the other hand, laser etching is much faster, highly precise, and does not require chemicals, making it an eco-friendly alternative. It also allows for better depth control, making it suitable for a wide range of applications. However, laser etching generates heat, which can lead to material discoloration or warping, especially on delicate metals. Cost is also a considerationβwhile chemical etching is cheaper for mass production, laser etching is preferable for small-batch and custom orders because it is flexible and has no setup fee. The decision between the two depends on the specific needs of the project, such as material, batch size, and desired detail level.
Which One Should You Choose?
The choice between chemical etching and laser etching depends on the specific requirements of your project:
Choose Chemical Etching If:
- You need highly detailed and precise patterns without material distortion.
- You are working with thin or delicate metals.
- You require cost-effective large-batch production.
Choose Laser Etching If:
- You need fast and precise marking for prototypes or small batches.
- You want variable depth control and flexibility.
- You prefer an eco-friendly process with no chemical waste.
Conclusion
Both chemical etching and laser etching have specific strengths that make them beneficial in precision metal manufacturing. Chemical etching performs well in high-precision, high-volume processing with thin metals, whereas laser etching is flexible, quick, and environmentally friendly for detailed markings. The strengths and limitations of each will enable manufacturers to make better-informed decisions for the optimal result for their specific applications.
Leave a Reply