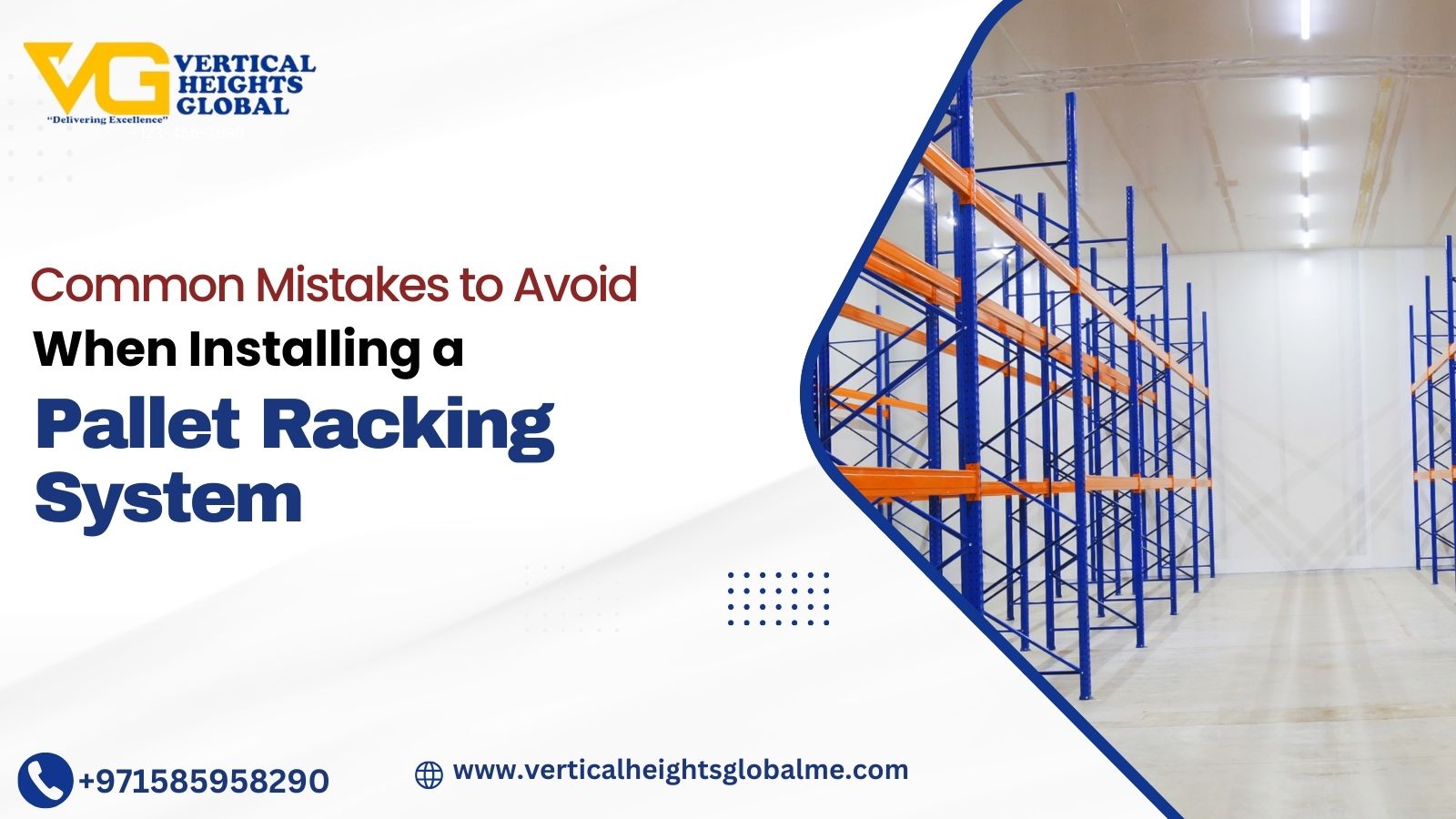
A pallet racking system is an essential component of any efficient warehouse, offering organized storage and easy access to inventory. However, improper installation or planning can lead to safety hazards, reduced efficiency, and unnecessary costs. To ensure your warehouse racking system operates effectively, itโs crucial to avoid common mistakes during installation. Here are key pitfalls to watch out for when setting up your warehouse storage racks.
1. Ignoring Load Capacity Limits
One of the most critical mistakes is overlooking the load capacity of your pallet racking system. Each racking system is designed to hold a specific weight limit. Exceeding this capacity can lead to structural failure, posing serious safety risks.
Tip: Always adhere to manufacturer guidelines and conduct regular load assessments to ensure compliance.
2. Poor Planning of Warehouse Layout
Improper layout planning can lead to inefficient use of space and hinder workflow. Failing to consider the size and shape of your inventory, as well as the movement of forklifts and other equipment, can cause congestion and slow down operations.
Tip: Before installing your warehouse racking system, create a detailed floor plan that maximizes storage space while ensuring smooth traffic flow.
3. Skipping Professional Installation
While it might be tempting to save costs with a DIY approach, improper installation can compromise the stability and safety of your warehouse storage racks.
Tip: Professional installers have the expertise to ensure that racks are assembled correctly, anchored securely, and aligned properly. Investing in professional installation can prevent costly mistakes and potential accidents.
4. Neglecting Safety Protocols
Failing to implement safety measures can result in accidents and damage to goods.
Tip: Ensure that your racking system includes safety accessories like rack guards, row spacers, and beam locks. Additionally, regular safety inspections and employee training on proper usage are essential to maintaining a safe warehouse environment.
5. Not Accounting for Future Growth
Many businesses focus solely on current storage needs without considering future expansion. This short-sighted approach can lead to additional costs and disruptions when itโs time to scale up.
Tip: Choose a pallet racking system that offers flexibility and can be easily modified or expanded as your business grows.
6. Incorrectly Anchoring the Racks
Anchoring your racks incorrectly or failing to anchor them at all can result in instability, especially in seismic areas or busy warehouses.
Tip: Secure anchoring is vital to prevent tipping or shifting, ensuring the long-term stability of your warehouse racking system.
7. Overlooking Clearance Requirements
Adequate clearance is essential for both safety and efficiency. Insufficient space between racks can hinder access, damage goods, and create hazards for employees.
Tip: Make sure to follow clearance guidelines for aisles, loading zones, and overhead space to facilitate easy navigation and safe operations.
Conclusion
Installing a pallet racking system requires careful planning and attention to detail to avoid common pitfalls that can compromise safety and efficiency. By understanding these mistakes and taking proactive steps, you can ensure a smooth installation process and a well-organized warehouse.
For expert guidance and high-quality warehouse racking systems, Vertical Heights Global offers tailored solutions that meet your specific needs. With their expertise, you can optimize your warehouse storage racks for maximum efficiency and safety.
Leave a Reply