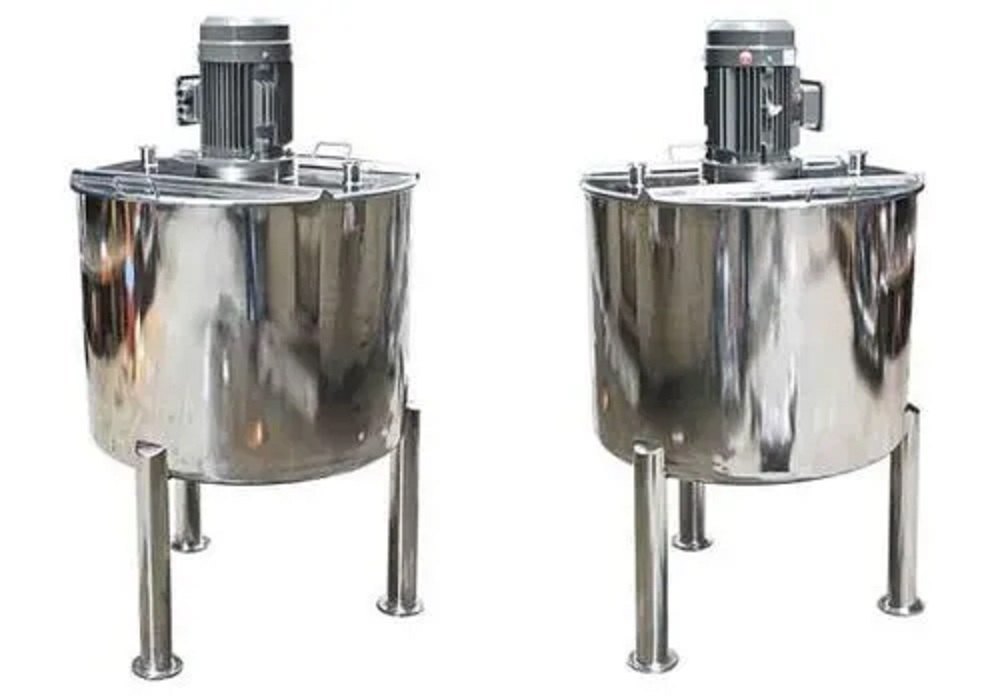
A mixing tank agitator is an essential component in industries that require efficient blending, suspension, or dispersion of materials. Agitators are used in industries such as pharmaceuticals, chemicals, food processing, and wastewater treatment to ensure uniform consistency in liquids, semi-solids, and powders. The selection of the right mixing tank agitator depends on factors like viscosity, volume, and the desired mixing process. This article explores various types of agitators and their applications in different industries.
Propeller Agitators
Propeller agitators are among the most commonly used types in mixing tank due to their high efficiency and ability to create a strong axial flow. These agitators consist of a three-blade or four-blade propeller that rotates at high speeds, generating a consistent flow pattern.
Applications:
- Used in the chemical and pharmaceutical industries for blending low-viscosity liquids
- Ideal for applications requiring rapid mixing of solutions and suspensions
- Commonly used in the food and beverage industry for juice and dairy mixing
Turbine Agitators
Turbine agitators consist of multiple flat or curved blades attached to a central hub. These agitators create radial and axial flow patterns, making them suitable for handling a wide range of viscosities.
Applications:
- Used in chemical reactors for emulsification and dispersion of immiscible liquids
- Common in fermentation and bio-processing applications
- Suitable for mixing paints, coatings, and adhesives where uniformity is essential
Paddle Agitators
Paddle agitators have wide, flat blades that rotate at relatively low speeds, making them ideal for mixing high-viscosity materials. These agitators are commonly found in applications where gentle mixing is required.
Applications:
- Used in wastewater treatment plants for slow-speed agitation of sludge
- Suitable for food processing applications like mixing batter and dough
- Ideal for blending suspensions and slurries in mineral processing
Anchor Agitators
Anchor agitators are designed with a central shaft and arms that extend to the walls of the mixing tank. This design prevents sedimentation and ensures even distribution of materials with high viscosity.
Applications:
- Commonly used in cosmetic and pharmaceutical industries for mixing creams and lotions
- Ideal for blending resins and adhesives in the chemical sector
- Used in the dairy industry for processing thick products like yogurt and cheese
Helical Ribbon Agitators
Helical ribbon agitators are designed with a helical blade that moves product both radially and axially, providing thorough mixing. These agitators are best suited for materials with high viscosity and require uniform blending.
Applications:
- Used in polymer and plastic manufacturing for blending viscous liquids
- Ideal for high-solid-content slurries in mining and metallurgical applications
- Common in food processing for making sauces, pastes, and confectionery
Magnetic Agitators
Magnetic agitators use a magnetically driven impeller instead of a mechanical shaft, reducing the risk of contamination and ensuring sterile mixing. These agitators are commonly used in industries where hygiene and precision are crucial.
Applications:
- Widely used in pharmaceutical and biotech industries for sterile mixing
- Ideal for food and beverage applications where contamination must be avoided
- Used in laboratory research for precision mixing of chemical solutions
High-Shear Agitators
High-shear agitators operate at high speeds to create intense turbulence and shear forces. These agitators are designed for breaking down solid particles, dispersing immiscible liquids, and homogenizing mixtures.
Applications:
- Used in emulsification of oil and water-based solutions in the cosmetic industry
- Common in the production of dairy products like creams and yogurt
- Ideal for breaking down powders and dissolving solids in the pharmaceutical sector
Static Mixers
Static mixers do not have moving parts but instead rely on the flow of the material through fixed geometric elements within the mixing tank. These mixers are energy-efficient and provide consistent blending without mechanical agitation.
Applications:
- Used in chemical processing for continuous mixing of reactants
- Ideal for water treatment plants for mixing chemicals with water
- Common in polymer manufacturing for ensuring uniform distribution of additives
Choosing the Right Mixing Tank Agitator
Selecting the best agitator for a mixing tank depends on multiple factors, including:
- Viscosity of the product: Low-viscosity liquids require high-speed agitators like propellers, while high-viscosity materials need slow-moving agitators like helical ribbons.
- Mixing purpose: Some processes require blending, while others involve suspension, heat transfer, or dispersion.
- Tank size and shape: The design of the mixing tank affects flow patterns, making certain agitators more effective than others.
- Process requirements: Industries with stringent hygiene requirements, such as pharmaceuticals and food processing, often prefer magnetic or high-shear agitators for precise control.
Conclusion
A mixing tank agitator plays a crucial role in ensuring the efficiency and quality of industrial mixing processes. With various types of agitators available, understanding their applications can help industries select the right solution for their needs. Whether it’s blending, emulsification, suspension, or homogenization, choosing the right agitator type ensures optimal performance and consistency in production.
Leave a Reply