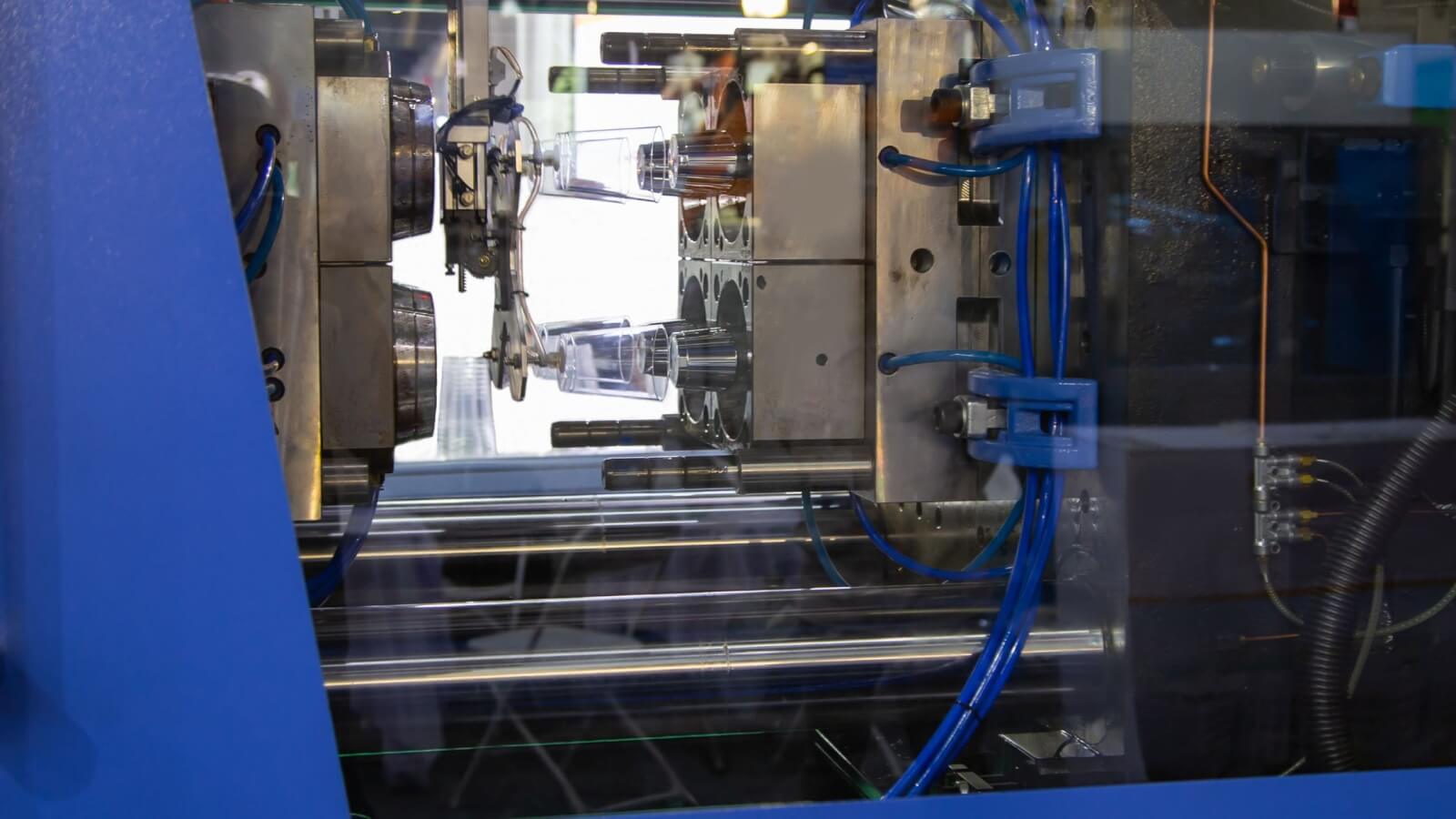
Introduction
Plastic injection molding is one of the most widely used manufacturing processes in modern industries. From automotive parts to household appliances, this technique plays a crucial role in producing high-quality plastic components efficiently and cost-effectively. Its ability to create complex shapes with precision and consistency has made it indispensable in various sectors, including medical, consumer goods, and electronics industries.
In this article, we will explore the fundamentals of plastic injection molding, its benefits, applications, and future advancements that are set to redefine the manufacturing landscape.
What is Plastic Injection Molding?
Plastic injection molding is a manufacturing process in which molten plastic is injected into a mold cavity under high pressure. Once cooled and solidified, the plastic takes the shape of the mold, resulting in a finished product. This process is ideal for mass production, enabling manufacturers to create thousands or even millions of identical parts with remarkable accuracy.
The Plastic Injection Molding Process
The process of plastic injection molding involves several key stages:
-
Clamping: The two halves of the mold are securely clamped together to withstand the injection pressure.
-
Injection: The plastic material, usually in the form of pellets, is melted and injected into the mold cavity through a nozzle.
-
Cooling: Once inside the mold, the plastic cools and solidifies, taking the desired shape.
-
Ejection: After cooling, the mold opens, and the finished product is ejected using ejector pins or plates.
-
Finishing: The molded part may undergo additional processes such as trimming, painting, or assembly before final use.
Benefits of Plastic Injection Molding
Plastic injection molding offers numerous advantages that make it the preferred manufacturing method for various industries:
-
High Efficiency and Speed
-
Once the mold is designed and set up, the production process is incredibly fast, allowing for large-scale manufacturing in a short time.
-
-
Consistency and Precision
-
Advanced computer-controlled machines ensure each part meets exact specifications, reducing errors and material waste.
-
-
Cost-Effectiveness
-
The ability to mass-produce identical components lowers production costs, making it an economically viable option for businesses.
-
-
Material Versatility
-
A wide range of thermoplastic and thermosetting materials can be used, allowing for customization based on strength, flexibility, or heat resistance requirements.
-
-
Minimal Waste and Sustainability
-
Excess plastic can be recycled and reused, making injection molding a more environmentally friendly manufacturing method.
-
Applications of Plastic Injection Molding
The versatility of plastic injection molding allows it to be used in diverse industries, including:
-
Automotive Industry
-
Dashboard panels, bumpers, and interior components are commonly manufactured using injection molding.
-
-
Medical and Healthcare
-
Syringes, prosthetics, surgical tools, and medical device housings are produced with high precision and biocompatible materials.
-
-
Consumer Electronics
-
Casings for mobile phones, laptops, and household appliances rely on injection molding for durability and aesthetic appeal.
-
-
Packaging Industry
-
Bottles, caps, containers, and food-grade packaging materials are efficiently produced using this technique.
-
-
Toys and Recreational Products
-
Popular toys, including LEGO bricks, are made through injection molding due to its ability to create detailed and durable parts.
-
Challenges and Solutions in Plastic Injection Molding
Despite its advantages, plastic injection molding has its challenges. However, continuous innovations help address these issues:
-
High Initial Tooling Cost
-
Solution: 3D printing and advanced CNC machining have reduced mold production costs, making small-batch production more feasible.
-
-
Material Limitations
-
Solution: Ongoing research in bioplastics and composite materials expands the range of usable plastics.
-
-
Environmental Concerns
-
Solution: The industry is shifting toward biodegradable plastics and sustainable manufacturing practices to reduce environmental impact.
-
Future Trends in Plastic Injection Molding
The future of plastic injection molding looks promising, with advancements in technology driving greater efficiency and sustainability:
-
Smart Manufacturing and Automation
-
The integration of AI and IoT in injection molding machines enables real-time monitoring and predictive maintenance.
-
-
3D Printing for Rapid Prototyping
-
Hybrid approaches combining 3D printing and injection molding allow faster prototyping and production iterations.
-
-
Eco-Friendly Innovations
-
Development of bio-based plastics and fully recyclable materials is gaining traction to reduce the environmental footprint.
-
-
Micro-Molding for Precision Components
-
The rise of micro-molding technology is enabling the production of miniature parts for medical and electronic applications.
-
Conclusion
Plastic injection molding has revolutionized modern manufacturing, offering a reliable, efficient, and cost-effective method for producing high-quality plastic components. With ongoing advancements in materials, automation, and sustainability, this technology continues to shape industries worldwide.
As we move toward a more environmentally conscious future, the evolution of plastic injection molding will play a crucial role in balancing industrial efficiency with sustainable practices, ensuring that high-quality products are manufactured responsibly and efficiently.
Leave a Reply