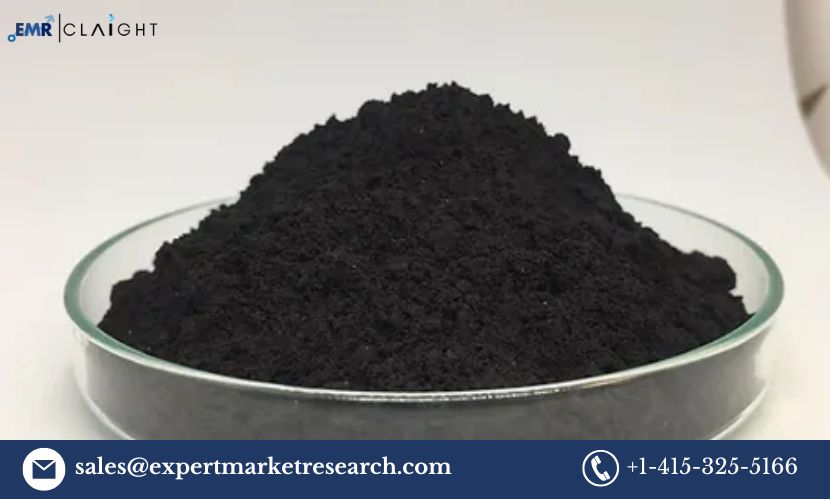
Introduction
Ferrite magnets, also known as ceramic magnets, are widely used in various industries due to their excellent magnetic properties, high resistance to demagnetization, and relatively low cost. These magnets are typically made from a combination of iron oxide (Fe2O3) and other metals such as barium or strontium. Ferrite magnet powders are the raw material for manufacturing these magnets, which find use in electric motors, sensors, loudspeakers, microwave equipment, and many other applications. The global demand for ferrite magnets is growing due to the increasing use of electronic devices and automotive components. The Ferrite Magnet Powder Manufacturing Plant presents a lucrative opportunity to meet this growing demand while capitalizing on the expanding electronics, automotive, and renewable energy sectors. This Ferrite Magnet Powder Manufacturing Plant Project Report outlines the key considerations for setting up a manufacturing facility, including market analysis, raw material sourcing, production processes, equipment requirements, cost analysis, and regulatory compliance.
Market Demand and Trends
The demand for Ferrite Magnet Powder is largely driven by several key factors:
-
Growth in Electronics and Electrical Industries: Ferrite magnets are widely used in the production of electrical motors, transformers, sensors, and magnetic components for electronic devices. As the demand for electronics and electrical devices continues to rise globally, the demand for ferrite magnets follows suit.
-
Automotive Industry: The increasing use of electric vehicles (EVs) and hybrid vehicles is driving demand for ferrite magnets in motors, actuators, and sensors. Ferrite magnets are used in electric vehicle motors due to their excellent performance in harsh conditions.
-
Renewable Energy Sector: Ferrite magnets are widely used in wind turbines, where they are essential for generating power efficiently. As the world moves toward renewable energy sources, the demand for ferrite magnets for use in wind turbine generators is expected to grow.
-
Consumer Goods: Ferrite magnets are used in speakers, headphones, microphones, and other consumer electronic products. The increasing demand for high-quality audio systems is contributing to the growth of the ferrite magnet market.
-
Cost-Effectiveness: Ferrite magnets are generally more affordable compared to other types of magnets, such as rare-earth magnets. This cost-effectiveness makes ferrite magnets a popular choice in a wide range of applications.
-
Globalization of Manufacturing: With industrialization and infrastructure development booming in emerging economies, the need for ferrite magnets is expected to increase. The development of new technologies and products requiring strong magnetic materials will further expand the market.
Given these trends, the establishment of a Ferrite Magnet Powder Manufacturing Plant presents a highly profitable venture that aligns with global demand across multiple sectors.
Get a Free Sample Report with Table of Contents@
Raw Materials and Sourcing
The primary raw materials used in the production of Ferrite Magnet Powder are:
-
Iron Oxide (Fe2O3): Iron oxide is the key ingredient in the production of ferrite magnets. It is sourced from naturally occurring ores and is processed to achieve the required purity for manufacturing magnets.
-
Barium Carbonate (BaCO3) or Strontium Carbonate (SrCO3): These materials are used to produce barium ferrite (BaFe12O19) or strontium ferrite (SrFe12O19) magnets, which are the two most common types of ferrite magnets. The choice of material depends on the specific application requirements and the desired magnetic properties.
-
Other Additives: Additional chemical elements such as cobalt, manganese, or zinc may be added in small quantities to modify the properties of the ferrite magnets, such as their coercivity, remanence, and magnetic permeability.
-
Solvents and Reagents: Various solvents and reagents are used in the synthesis of ferrite magnet powders, including acids and bases for chemical reactions and purification steps.
-
Packaging Materials: Packaging materials such as plastic bags, drums, or containers are required to store and ship the ferrite powder to customers or other manufacturers.
Manufacturing Process
The process of manufacturing Ferrite Magnet Powder involves several key steps, each essential for ensuring high-quality powder that can be used in the production of ferrite magnets. Below is a detailed description of the production process:
1. Preparation of Raw Materials
The first step in the production of ferrite magnet powder is the preparation of the raw materials. Iron oxide and barium or strontium carbonate are carefully weighed and mixed to create a homogeneous mixture. Depending on the desired type of ferrite (barium ferrite or strontium ferrite), the appropriate combination of raw materials is selected.
-
Iron Oxide: Iron oxide is typically sourced from natural iron ore, which is processed to remove impurities and achieve the necessary quality.
-
Barium or Strontium Carbonate: These chemicals are typically produced synthetically and must be of high purity to ensure the best magnetic properties.
2. Sintering (Calcination)
The next step involves sintering, which is a high-temperature process that transforms the mixture of iron oxide and barium or strontium carbonate into a ferrite material. This process is carried out in a furnace at temperatures typically ranging from 1000°C to 1200°C.
-
Furnace: The sintering process occurs in a rotary kiln or a tunnel furnace, where the raw mixture is heated in a controlled atmosphere. During sintering, the carbonates react with iron oxide to form a crystalline ferrite structure.
-
Calcination: The sintering process also helps eliminate any residual moisture and other volatile substances from the mixture.
3. Milling and Grinding
Once the ferrite material has been sintered, it is allowed to cool before being milled into a fine powder. The size of the powder particles is critical to achieving the desired magnetic properties, so precise milling and grinding processes are essential.
-
Ball Mill: A ball mill is commonly used to grind the sintered ferrite into a fine powder. The grinding process may take several hours to ensure that the powder is of the desired particle size.
-
Air Classifier: After milling, the ferrite powder is passed through an air classifier to separate fine particles from coarse ones. Only the fine powder with the correct particle size distribution is used for manufacturing magnets.
4. Magnetization
After grinding, the ferrite powder is ready to be magnetized. This is done by subjecting the powder to a strong magnetic field to align the particles and enhance their magnetic properties.
-
Magnetic Field Application: The powder is placed in a strong magnetic field, where the particles align to create a strong, uniform magnetic charge.
-
Magnetic Properties Testing: The magnetized powder is tested for its coercivity, remanence, and magnetic permeability to ensure that it meets the required specifications.
5. Packaging
Once the ferrite magnet powder has been produced and tested, it is packaged for shipping. Packaging is done in sealed bags or containers that protect the powder from contamination and moisture.
- Sealed Packaging: The powder is carefully weighed and packaged to prevent contamination, ensuring that it remains stable until it reaches its destination.
Infrastructure and Equipment
To set up a Ferrite Magnet Powder Manufacturing Plant, the following infrastructure and equipment are required:
-
Raw Material Handling and Storage: Facilities for storing and handling raw materials such as iron oxide, barium carbonate, and other additives.
-
Sintering Furnace: A high-temperature furnace for sintering the raw materials to form ferrite compounds.
-
Ball Mills and Grinding Equipment: For milling and grinding the sintered material into a fine powder.
-
Air Classifiers: To separate fine particles from coarse ones after milling.
-
Magnetization Equipment: Equipment for applying a magnetic field to the ferrite powder to enhance its magnetic properties.
-
Quality Control Lab: A lab for testing the quality of the ferrite powder, including particle size analysis, magnetic property testing, and purity checks.
-
Packaging Area: A designated area for packaging the final ferrite powder into sealed containers for shipment.
Cost Analysis and Financial Planning
Setting up a Ferrite Magnet Powder Manufacturing Plant involves various costs:
-
Initial Capital Investment:
- Building and Infrastructure: Construction or leasing of the plant facility and required infrastructure.
- Machinery and Equipment: The cost of sintering furnaces, grinding mills, air classifiers, and magnetization equipment.
-
Operating Costs:
- Raw Materials: Procurement of iron oxide, barium or strontium carbonate, and other chemicals.
- Labor: Hiring skilled workers, including chemical engineers, technicians, and machine operators.
- Energy Costs: High energy consumption due to the sintering process and grinding operations.
-
Revenue Generation: Revenue is generated from the sale of ferrite magnet powder to manufacturers of magnets, electronic devices, automotive components, and other industries requiring magnetic materials.
Regulatory Compliance and Environmental Considerations
-
Environmental Impact: The plant must comply with local environmental regulations regarding emissions, waste disposal, and the use of hazardous materials. Proper handling and disposal of chemicals and solvents used in the process are essential.
-
Regulatory Approvals: The plant must obtain necessary licenses and certifications from local regulatory bodies for manufacturing chemical products and ensure the final product meets industry standards.
-
Product Safety and Quality Assurance: The plant must adhere to strict quality control guidelines to ensure that the ferrite powder produced is safe, non-toxic, and meets the required magnetic properties.
Media Contact
Company Name: Claight Corporation
Contact Person: Lewis Fernandas, Corporate Sales Specialist — U.S.A.
Email: sales@expertmarketresearch.com
Toll Free Number: +1–415–325–5166 | +44–702–402–5790
Address: 30 North Gould Street, Sheridan, WY 82801, USA
Website: www.expertmarketresearch.com
Aus Site: https://www.expertmarketresearch.com.au
Leave a Reply